The 6 Steps to Distillation Column Design
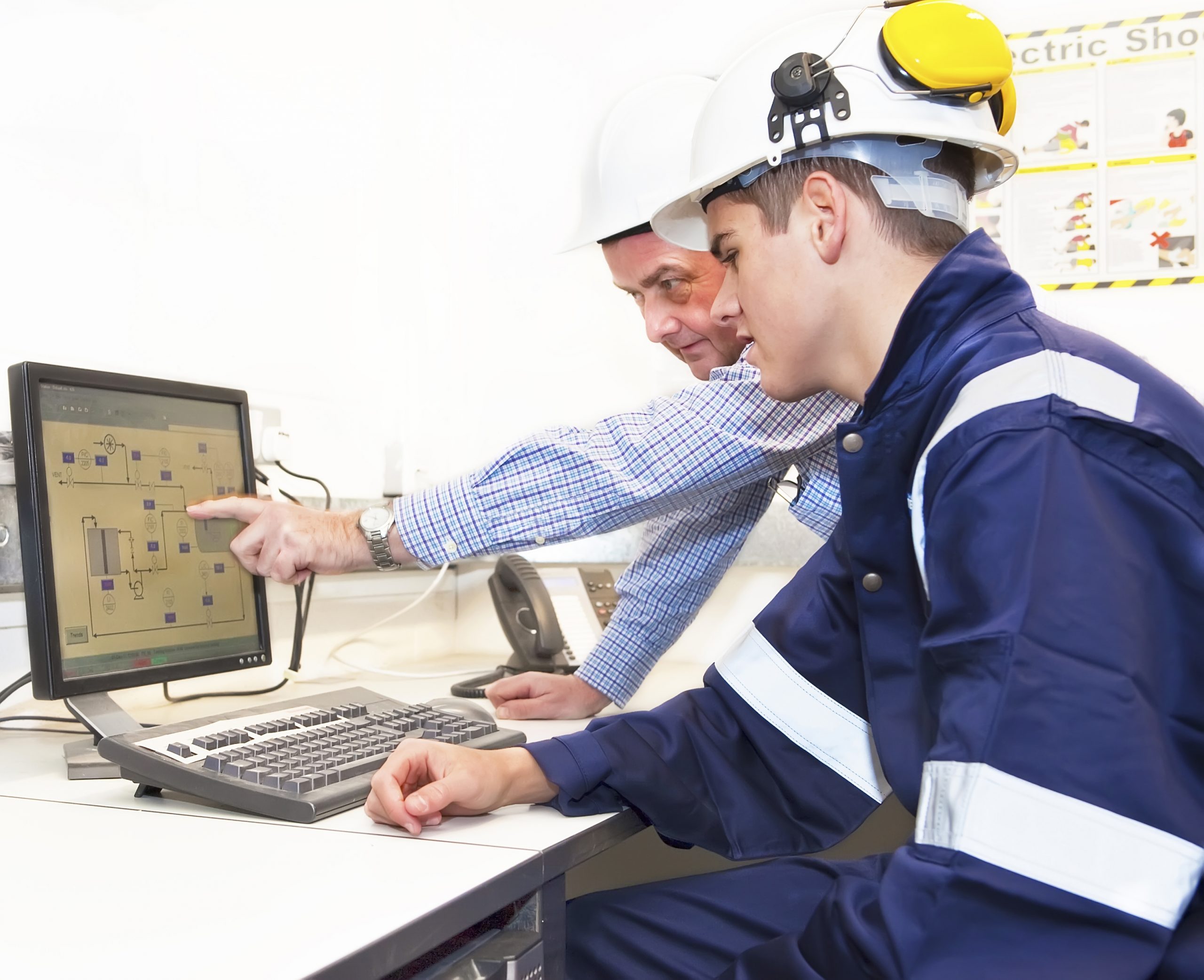
Here at AMACS, we love to write about Distillation Columns and how our products can improve performance, especially during shutdowns and turnarounds. However, it is also important to understand the design process for distillation columns to get your products to your desired purity. This is usually done via boiling a mixture, working with vapors, and doing it all at the lowest cost possible. To help, we will share the basic 6 steps to distillation column design.
- Determine Your Product Specifications
What is your ideal final product? This is usually determined by selecting your recovery feed percentage, your product’s composition, and the physical properties of your desired product or products. This includes both heavy and light components.
- Select the Optimal Operating Pressure
Operating pressure must be expertly and carefully selected, as it has an effect on the entire column, as well as the final product. Remember that as operating pressure goes up, needed stages go up, volatility can go down, exchanger sizes go down, and separation is harder. In all, the column can and does become more costly as pressure goes up.
It all depends on the process. For example, a debutanizer that separates butane from natural gas usually operates at 70 yo 80 psi. Alternatively a deethanizer that removes ethane from refinery gas streams operates at 375 to 450 psig.
- Select Vapor Liquid Equilibrium
Your VLE defines the distribution of a chemical between the vapor and liquid phase. Many factors go into selecting a VLE including:
- Data on enthalpy, or the energy measure in your column with a thermodynamic quantity equivalent to the total heat content.
- Columns that operate at near boiling temperatures can be difficult to operate.
- We recommend you invest in the right data, models, and methods to achieve the best results.
Additionally, we recommend using the advice of experts, engineers, and even contractors to ensure your VLE is ideal.
- Select Best Number and Efficiency of Your Trays
AMACS knows all about the importance of column internals, including trays for distillation columns. You ideally want the least number of trays, which can be calculated by various equations, such as Fenske, DISTWU, and others. Tray efficiency is also determined by a number of complex calculations. One of the best ways to learn for yourself is to attend an expert program, such as Practical Distillation Technology from Kister.
- Tower Internal Selection
As in the above, AMACS also has experience with other internals. You may require internals for distillation columns that include structured packing, random packing, wedge wires, and many others. These internals are often designed to control pressure drop, fouling, turndown requirements, and more. It is essential to make the right choice here for ideal operation, output, and to minimize operating costs.
- Final Steps
Even though these are the major steps, there are other factors to distillation column design.
These include:
- Determining the ideal diameter of the tower using the above data.
- Select your tray spacing, as well as how many tray passes using the above data.
- Other items such as downcomer, tray drop, weir height, and others.
We at AMACS have extensive experience in helping organizations properly select trays, packings, and other column internals with a specialization on shutdowns and turnarounds. Contact us to help you effectively design distillation columns or improve existing ones.