Optimizing Work Scope for Effective Turnaround Management
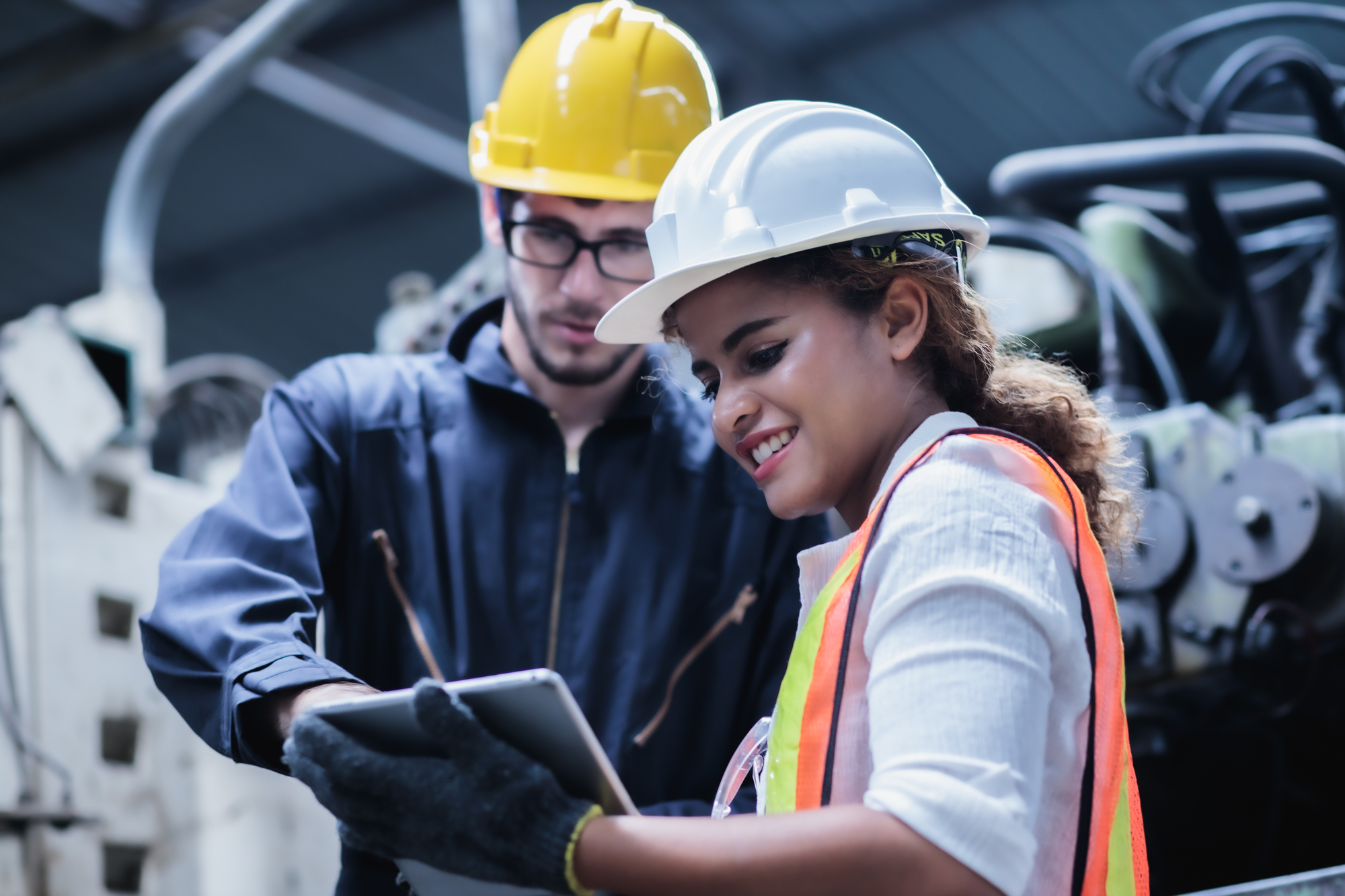
The Critical Role of Work Scope in Turnarounds
Plant turnarounds are among the most complex and high-stakes projects in industrial operations, requiring meticulous planning, execution under strict deadlines, and seamless coordination among multiple stakeholders. With turnaround costs often exceeding $1 million per day in lost production and expenses, any deviation from the schedule can result in severe financial consequences.
One of the most significant factors determining the success or failure of a turnaround is the work scope—the detailed plan outlining the tasks, objectives, and contingencies required to complete the project efficiently. However, work scopes are notoriously dynamic, often requiring mid-turnaround modifications due to unforeseen challenges such as unexpected equipment failures, safety hazards, or supply chain disruptions. A rigid or incomplete work scope can introduce costly inefficiencies, while an overly flexible one can lead to scope creep and uncontrolled delays.
Challenges in Creating an Effective Turnaround Work Scope
Developing a turnaround work scope is a complex process that must balance predictive planning with real-time adaptability. According to industry research, 70% of turnaround projects experience budget overruns, with scope changes being one of the primary causes. Several challenges contribute to these overruns:
- Incomplete or Inaccurate Initial Work Scope
Many plants underestimate the true scope of necessary repairs and upgrades because certain issues—such as corrosion, material fatigue, or fouling—are only detected after equipment disassembly. This leads to reactive decision-making that can delay procurement and execution.
- Scope Creep Due to Unplanned Additions
While some modifications during execution are unavoidable, excessive add-ons disrupt logistics, labor availability, and material supply. Studies indicate that scope growth of more than 10% increases turnaround delays by an average of 20%, as crews are forced to adjust work schedules on the fly.
- Decision-Making Bottlenecks
A well-structured turnaround depends on rapid decision-making. However, conflicting priorities between operations, maintenance, and contractors can cause delays in approving scope changes. Without a streamlined approval process, critical decisions—such as whether to replace a damaged heat exchanger tray or extend cleaning schedules—become major roadblocks.
- Supply Chain and Material Shortages
The availability of spare parts, specialized equipment, and replacement internals is often a limiting factor. A delay in receiving critical components can extend turnaround schedules by several days or even weeks. Many successful facilities now preemptively source high-risk replacement parts to mitigate such risks.
- Misalignment with Primary Turnaround Objectives
Not all scope changes align with the core business objectives of the turnaround. For example, a planned inspection may lead to additional non-essential upgrades, diverting resources away from more pressing reliability issues. Ensuring strict scope discipline is essential to prevent unnecessary cost escalation.
The Consequences of Poor Work Scope Planning
When work scope deficiencies arise, the ripple effects are immediate and widespread:
- Schedule overruns—With each additional unplanned task, turnaround schedules stretch, impacting downstream operations.
- Escalating costs—Every extra day of downtime means lost revenue. In refining and chemical processing, one day of extended turnaround can result in millions in lost production value.
- Logistical chaos—Poorly managed work scope results in conflicting work orders, uncoordinated contractor activities, and inefficient workforce utilization.
- Employee morale declines—Engineering and operations teams working under unclear direction experience frustration, reducing productivity and efficiency. Common complaints include “we’re running in circles” and “this turnaround was worse than the last one.”
Best Practices for Structuring an Effective Turnaround Work Scope
To ensure optimal execution, a robust and adaptable turnaround work scope must be developed well in advance. The following best practices have proven to reduce scope-related issues and improve turnaround efficiency:
- Cross-Departmental Collaboration in Work Scope Development
An effective work scope is not solely a maintenance plan—it must integrate insights from operations, engineering, procurement, and safety teams. Facilities that involve all departments early in the planning process report 20-30% fewer last-minute scope changes.
- Built-in Flexibility Without Unchecked Growth
A structured change management process ensures that necessary modifications can be made without derailing the turnaround timeline. Work scopes should predefine contingency actions for potential equipment failures or inspection surprises.
- Clear Role Definitions for Contractors
Third-party contractors play a critical role in turnarounds, but unclear expectations can lead to workflow inefficiencies and disputes. Clear delineation of responsibilities ensures that contractors can quickly mobilize teams without waiting for managerial approvals.
- Contingency Planning for Supply Chain Disruptions
Given that 40% of turnaround delays stem from material shortages, securing long-lead-time parts before shutdowns begin can mitigate unnecessary downtime. Plants that preemptively order replacement column internals, trays, and mist eliminators have significantly lower unplanned delays.
- Deadline Commitments from Each Department
Strict but realistic deadlines ensure accountability. Effective turnaround teams operate with milestone tracking systems to ensure that no department falls behind.
- Alignment with Business Objectives
Work scope planning should continuously tie back to the primary objectives of the turnaround—whether it’s reliability, throughput optimization, or regulatory compliance. Any proposed scope additions should be evaluated against these priorities before approval.
Choosing the Right Contractors for Turnaround Success
A critical component of turnaround success is partnering with highly experienced contractors who can deliver results under tight schedules. Given that some turnarounds can exceed $100 million in costs, choosing the wrong vendor can be an expensive mistake.
AMACS has been a trusted supplier of process column, tower, and vessel internals for over 70 years. Our Houston, Texas manufacturing facility specializes in:
- Custom mist eliminators, coalescer elements, and fractionation trays
- Structured, random, and grid packing solutions
- Tray hardware, liquid distributors, and packed bed supports
- Rapid turnaround manufacturing for replacement internals
With a proven track record of delivering critical components within days—not weeks—AMACS helps facilities minimize turnaround downtime.
Partner with AMACS for Your Next Turnaround
For facilities preparing for an upcoming turnaround, AMACS offers consultation and rapid manufacturing solutions to ensure your plant is back online as quickly and efficiently as possible.
📞 Contact us today to discuss your turnaround needs with our experienced engineering team. Let us help you develop a work scope strategy that minimizes delays and maximizes efficiency.