The Importance of Preventing Tray Damage in Distillation Columns
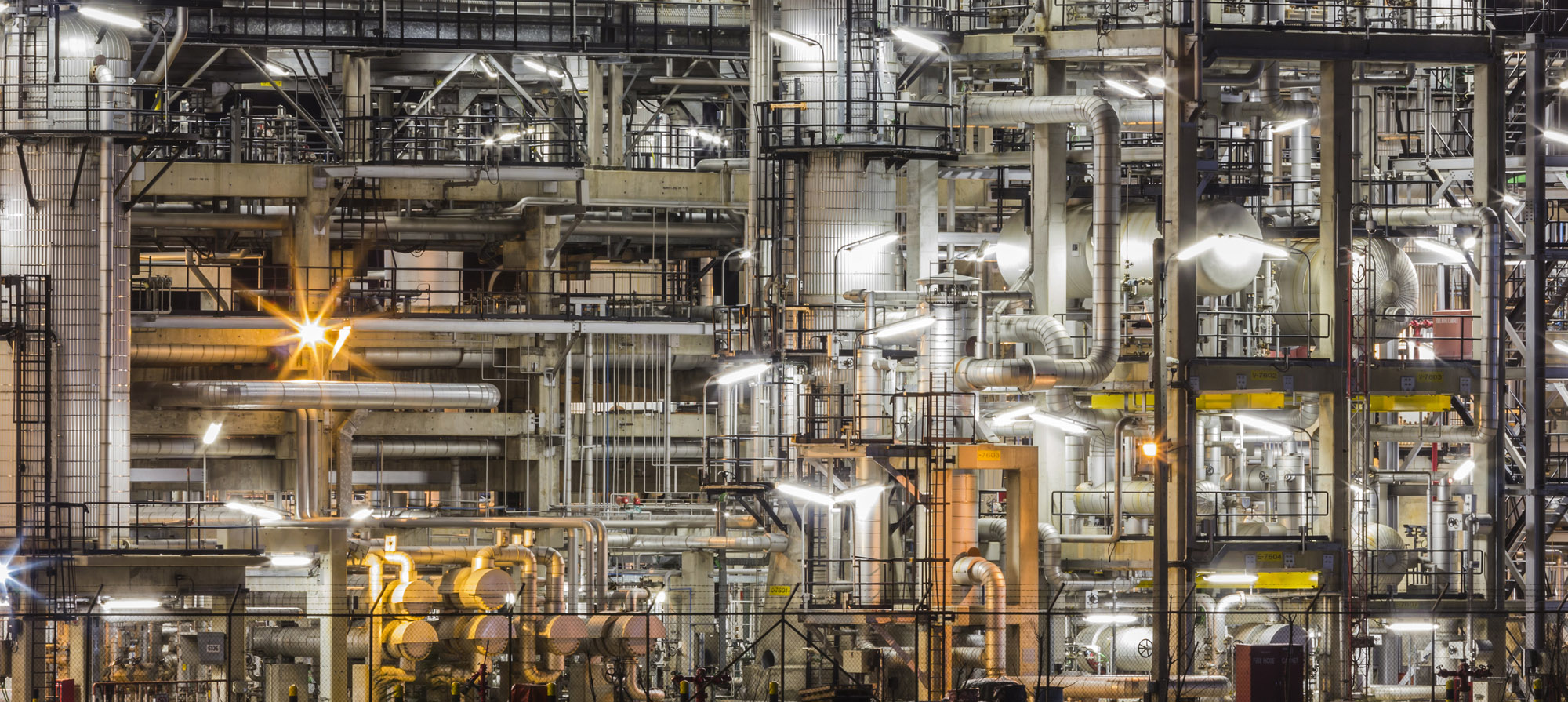
Preventing tray damage in distillation columns can come with a heavy cost, but it is worth it. Tray damage can end up causing a limited production operation, if not a complete shutdown, especially in high throughput processes. Below we will discuss the importance of preventing tray damage in distillation columns, what causes it, how to diagnose it, and how to avoid it.
The Cost of Tray Damage in Distillation Columns
The immediate expenses for tray damage include the immediate costs to dismantle and repair the columns. This can include any expenses with hiring experts to dismantle, diagnose, and repair the column. Often times, costs also include purchasing new trays, packings, or other components that were damaged during the breakdown. In addition, the damage may have occurred due to a faulty setup. In these cases, other experts must be hired to correctly configure the distillation columns. Finally, there is always a substantial cost in lost production, no matter how brief.
Most Common Tray Damage Causes in Distillation Columns
Science Direct conducted a survey of 17 occurrences of tray damage in columns. The columns included anywhere from 20 to 60 trays and had diameters from 30 to 144 inches. The results for the most common causes of damage where:
For operating errors in 14 columns:
- High liquid in the bottom caused 72% of failures.
- Vacuum issues in 21% of failures.
- High vapor rate in 7% of failures.
For total number of incidents in 18 columns:
- High liquid in the bottom for 56% of failures.
- Vacuum issues in 17%.
- Installation and corrosion in 22%.
- High vapor rate in 5%.
Other causes of tray damage included dry trays, flooded trays, miscellaneous damage to trays, and more.
Signs of Tray Damage in Distillation Columns
Some tray damage can be spotted before a partial or complete breakdown occurs. For example, fluctuations in the column and pressure disturbances may be caused by tray damage. Other signs of tray damage include fouling, plugging, foaming, measurement errors in vital operating parameters, and instability caused by improper controller tuning. Finally, tray damage can also be noted by feed rate changes, feed composition changes, and steam quality variations or steam supply pressure.
How to Diagnose Tray Damage in Distillation Columns
Each column is different, but there are some general rules to diagnosing damage. The first step to confirm that control loops and measurement instruments are functioning properly. Second, check the feed rate, steam rate, reflux rate, temperatures, and other variations when the column is unstable. If neither of these addresses the issue, the cause is most likely internal. You may look for signs as in the above, or contact an expert in your area who can help diagnose and repair your column.
AMACS Can Help with Diagnosing and Preventing Tray Damage in Distillation Columns
We know it can be frustrating for those of you who have spent considerable time and expense to implement an advanced distillation column strategy to save thousands to millions per year to have all that lost because as the result of tray damage. We at AMACS are experts in trays and tray damage for distillation columns and are a leading Gulf Cost provider of many other column internals. AMACS can help you get your columns performing their best through our expertise in selecting the correct trays needed for your operation. Contact AMACS today to see how we can help prevent tray damage.