Wedge Wire Industrial Screens & Their Benefits
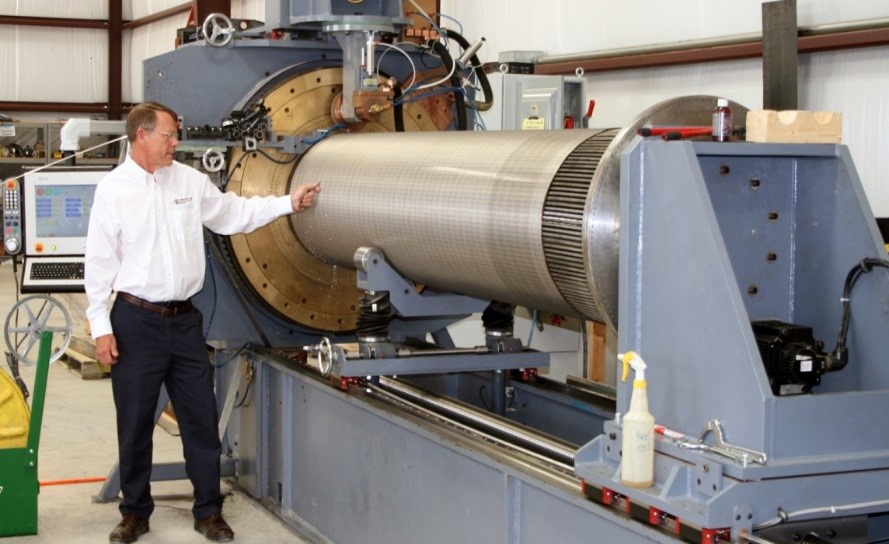
Industrial processes and applications are numerous and complex. What do you do when you have an application that is highly specific and no traditional solution seems to work? You turn to a non-traditional solution. Below, we will discuss wedge wire screen products, their benefits, as well as what applications can utilize them.
What is a Wedge Wire Industrial Screen?
Wedge wire industrial screens are made by wrapping “V” shaped profile wire around longitudinal support ribs. All the wires and ribs are resistance welded at each contact point to create a structurally sound plug resistant surface. The numerous combinations allowed by wedge wire screens allow for exact matches to technical specifications. They are available in almost any alloy and can be used in industries such as water treatment, food and beverage, oil and gas, pulp and paper, mineral and aggregate processing, and petrochemical.
Types of Wedge Wire Industrial Screens
Catalyst Bed Supports – These screens feature durable construction, a precise open area, and near non-clogging. Their support grids provide superior media retention in vessels of all types. Larger vessel diameters have grids manufactured in sections to accommodate installation for man ways. They can come with an inlet basket or distributor lateral, support grid, and outlet basket with backwash systems.
Hub and Header Laterals – These screens may be used for disc head vessels that need the system to completely collect to the vessel bottom. Header lateral design can also be used in flat bottom vessel distributor or collector applications. Screens can accommodate side, center, top, or bottom inlet piping. Hub and header laterals can also come with integral backwash systems for fast and effective cleaning. Systems can be designed for liquid or solid retention for applications including exchangers, clay and sand filtration applications, carbon towers, and power plants with water systems.
Nozzles & Strainers – Retention nozzles can be made to flow requirements in almost any alloy. They can be designed for filtration or treatment systems to permit more use of the media. Non-clogging wedge wire nozzles are used in water treatment and other industrial applications, such as under drain media retention elements, flow distributors in demineralizers, water softeners in pressure, and gravity sand filters. They may also be used as bottom vessel collectors across a tray plate with a high open area and non-plugging design.
Sieve Bend and Flat Screen – Those who need high capacity filtration will enjoy this option where the screens are also durable, reusable, and self-cleaning. Sieve Bend screens can allow water to drop through the screen for collection while the angle and flow allow solids to slide over. These screens are ideal for wastewater treatment, dewatering, and sewage separation systems.
Resin Trap Screens – The screens are generally placed in housing that is inline with flow to keep expensive media from flowing downstream. Traps may be designed to capture particles in any size with a sufficient open area to let the process flow smoothly.
AMACS is a leader in designing wedge wire industrial screens, as well as manufacturing them to a custom requirements and specifications. Contact us if you believe our AMACS’ wedge wire screens may be right for your operation or you would like to learn more about how they can help!