The Top 3 Leadership Factors in Turnarounds: A Guide for Turnaround Managers, Engineers, and Plant Managers
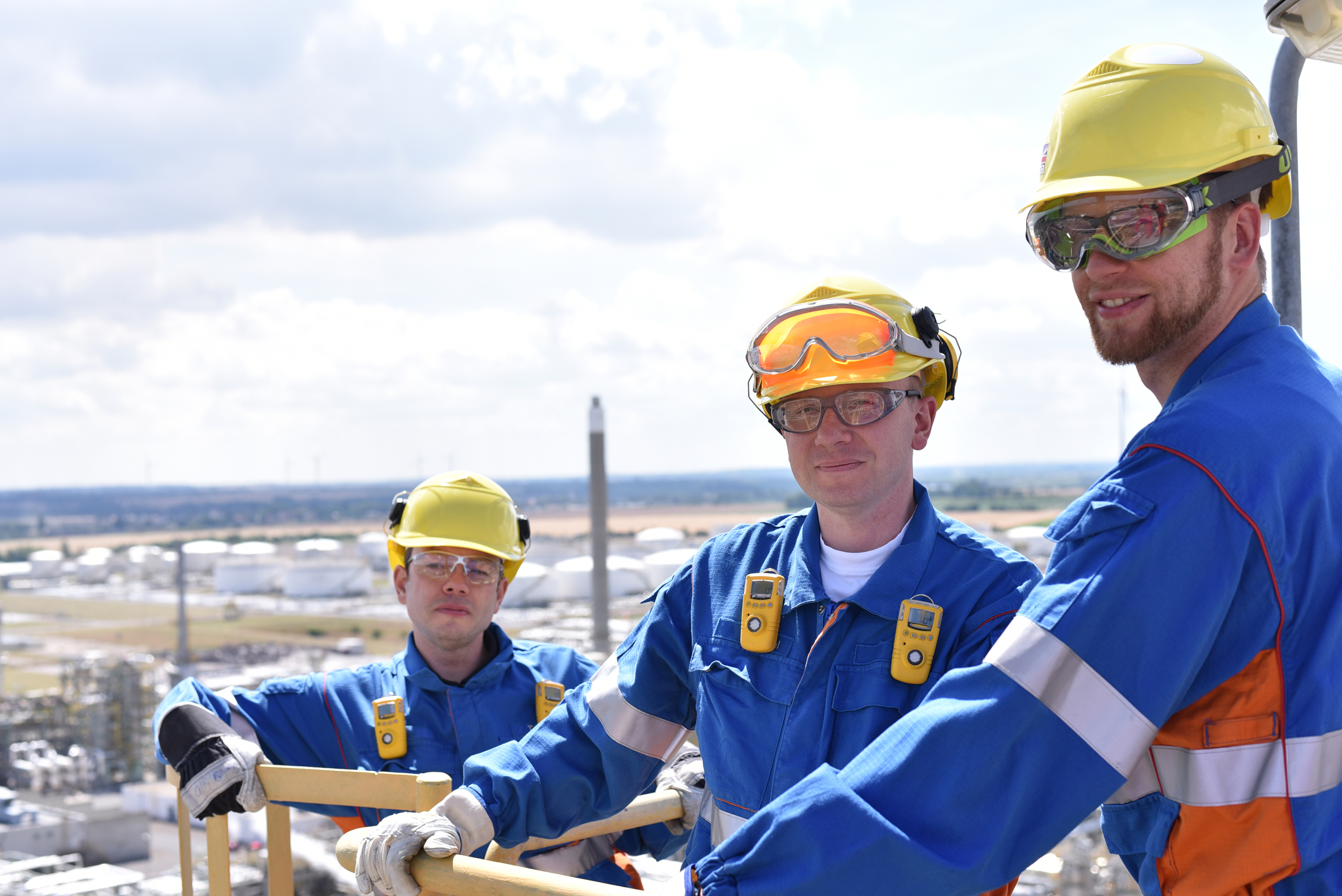
In the world of industrial turnarounds, leadership is paramount. A turnaround, whether for a production facility, refinery, or manufacturing plant, demands leadership that goes beyond traditional management practices. John O. Whitney, a recognized expert in leadership and management during turnarounds, emphasizes that “how the new leader solves these problems when his predecessors have failed will be the result of a skilled blend of style and substance.” His insight is invaluable for professionals such as Turnaround Managers, Maintenance Engineers, Reliability Managers, Reliability Engineers, and Plant Managers, who face the intricate challenge of turning a plant or facility around, often under intense pressure and time constraints.
Whitney also stresses that leadership in a turnaround is vastly different from day-to-day operations, and we wholeheartedly agree. Turnarounds require a distinct approach, with a clear focus on resolving issues, inspiring teams, and executing strategic changes swiftly. Below, we delve into the essential leadership qualities that drive successful turnarounds and explain why they matter to professionals in key leadership roles.
Key Leadership Qualities for Turnarounds
While leadership in turnarounds is never one-size-fits-all, certain characteristics consistently emerge as essential for success. These qualities are not merely theoretical; they are practical traits that allow leaders to navigate the complexities and high-stakes environments of turnarounds. Here are the top qualities of successful turnaround leaders:
- People Skills
Turnaround leaders must be adept at connecting with diverse teams, from contractors to plant personnel. Clear communication is key, as is fostering an open-door policy that encourages feedback and transparency. A leader who is approachable and able to both give praise and deliver constructive critique ensures that morale stays high and performance improves. In technical environments, where complex systems and operations require collaboration, strong people skills are non-negotiable. - Decisiveness with Data-Driven Insight
In a turnaround scenario, hesitation can be costly. The ability to make well-informed decisions quickly is essential, particularly when dealing with production bottlenecks, equipment failures, or process inefficiencies. However, strong turnaround leaders do not rush into decisions without understanding the underlying data. They gather the necessary information from various departments—such as maintenance, production, and operations—before making decisions, ensuring they are backed by facts and clear reasoning. This balance of data-driven insights and decisiveness helps maintain control and momentum throughout the turnaround process. - Adaptability and Innovation
Turnarounds require leaders to challenge the status quo. Often, old systems, outdated practices, or inefficient processes have contributed to the plant’s current state, and innovation is the key to recovery. A turnaround leader must foster an environment of continuous improvement, encouraging new ways of solving problems and implementing solutions. This includes reevaluating existing workflows, introducing new technologies, or even rethinking safety protocols. Leaders who insist on doing things “the way they’ve always been done” risk stalling progress. Innovation involves both a willingness to question established methods and the courage to implement changes that can drive substantial improvements.
Leadership Approach in Turnarounds: The Hands-On, Budget-Savvy, and Confidence-Building Leader
Turnaround leadership is fundamentally about driving results under challenging circumstances. Good leaders understand that their role goes beyond strategic oversight—they need to be hands-on, closely involved in operations, and exhibit financial acumen. These factors help build trust and ensure that the turnaround stays on track.
Hands-On Involvement and Direct Engagement
Successful turnaround leaders do not sit idly in boardrooms. They actively engage with all critical processes and maintain visibility across the operation. Whether overseeing equipment inspections, ensuring maintenance tasks are completed on time, or handling operational challenges, these leaders are in the field with their teams. Their hands-on involvement allows them to identify issues in real-time, make timely decisions, and reinforce their commitment to the project’s success. Knowledge of key metrics such as downtime, equipment performance, and operating costs is essential. A leader who is familiar with these numbers and actively tracks them can quickly detect discrepancies and address them before they escalate into major issues.
Effective Budget Management and Cost Control
During a turnaround, financial discipline is critical. Leaders must be prepared to manage resources efficiently and make tough decisions regarding expenditures. Key actions include:
- Implementing strict yet reasonable controls over operating expenses, ensuring that every dollar is accounted for and spent wisely.
- Reevaluating and re-approving purchase orders: Any spending approved by previous managers should be re-assessed, and only necessary purchases should be authorized.
- Reviewing ongoing capital projects: A thorough analysis of all capital projects should be conducted to determine if they should be continued, adjusted, or canceled to better align with turnaround goals.
- Freezing unnecessary expenses: This might include salary freezes or restricting new hires and contractor agreements to prevent overspending.
Leaders who effectively manage the budget ensure the project stays financially viable, mitigating risk while driving progress.
Building Confidence in the Workforce and Stakeholders
As highlighted by Rosabeth Moss Kanter, a noted expert on organizational leadership, confidence in both management and the workforce is a cornerstone of any successful turnaround. Workers need to believe not only in their own abilities but also in the ability of their colleagues and leadership to bring about change. Confidence is especially critical when interacting with external stakeholders, including investors, auditors, and regulatory bodies. The leader’s role is to inspire this confidence through transparency, respect, and collaboration.
Kanter observed that a negative cycle—where blame is assigned, secrecy prevails, and individual isolation occurs—can derail a turnaround. Conversely, successful turnaround leaders replace secrecy with open dialogue, blame with respect, and isolated decision-making with inclusive collaboration. They cultivate an environment where employees feel empowered, and management’s direction is understood and supported.
Why Leadership Style Matters in Turnarounds
The leadership qualities discussed above are crucial because turnarounds are high-stress environments that require agility, resourcefulness, and strategic foresight. The leader’s style—whether they take an authoritative, participative, or delegative approach—will significantly influence the plant’s performance during the turnaround. The right leader adapts their style to the needs of the situation, blending strong decision-making with collaborative input and innovative thinking.
However, it’s essential to recognize that there is no one-size-fits-all leadership style for turnarounds. The most effective turnaround leaders understand their team, the specific challenges they face, and the plant’s unique operational dynamics. In this context, the combination of technical expertise, leadership acumen, and emotional intelligence creates a dynamic leader who can drive the team toward success.
Building a Successful Turnaround with Strong Leadership
In a turnaround, leadership is the force that can drive recovery, foster collaboration, and build trust. The key qualities that successful leaders exhibit—people skills, decisiveness, innovation, and budgetary control—are not just about leading a team, but about transforming the plant culture and setting the groundwork for future success.
At AMACS, we understand the critical factors that influence successful turnarounds. With over 40 years of experience, our team is equipped with the knowledge and resources to support your turnaround goals. From providing replacement equipment to engineering advanced solutions, we are committed to assisting with all your plant’s internal needs. Contact our turnaround experts 24/7 to discuss how we can help optimize your operations and ensure a successful turnaround.