The Importance of Work Scope in Turnaround Management
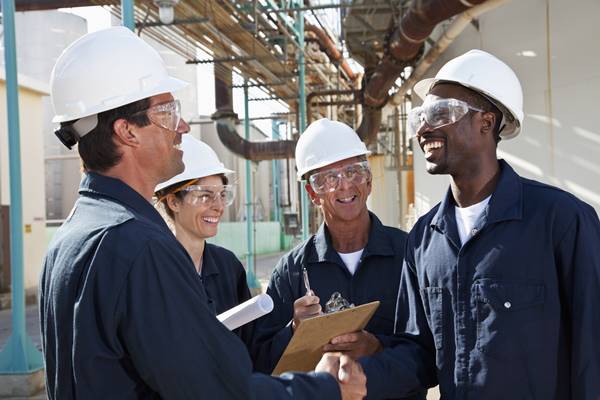
Turnarounds are always sizable projects that must be executed under strict time constraints with severe financial consequences for any delay. They are also subject to significant work scope changes that can be the result of unplanned issues arising during the turnaround. Rapid decisions must be made and approved, a task that is inadvisable but necessary during this time. In far too many instances, rash decisions can be costly and add further delay.
Challenges of Creating a Turnaround Work Scope
There are many challenges when creating an effective work scope strategy. For example, some issues may not be known until inspections are performed. For instance, equipment can be damaged during the turnaround, especially during moving and disassembly. Having a fluid work scope strategy that emphasizes preparation and the ability to act quickly and wisely in unplanned scenarios is key.
Common issues that make a work scope strategy fall short include:
- Work scope does not encompass all aspects of the turnaround
- Additions to work scope that were unplanned
- Excessive additions to work scope after it is complete
- Delays in making effective decisions regarding new work
- Shortages in materials and equipment
- Strategy of work scope does not conform to the primary objective(s) of the turnaround
Results of a Poor Turnaround Work Scope
A result of these inefficiencies in the work scope is higher risk in the speed and results of the turnaround. Signs of a poorly planned work scope range from conflicting control documents and schedule plans to issues between plant workers and contractors.
Staff morale is also critical to having work performed efficiently and effectively. Phrases you don’t want to hear during a turnaround include “we’re running in circles,” “catch-22,” “we’re always fighting fires,” and “the plant was better off a decade ago.” When asked the underlying cause of a turnaround failure, many managers blamed poor focus on objectives, undefined execution plans, and constant changes in the work scope.
Components of an Effective Turnaround Work Scope
To achieve the best outcome, plants must prioritize the development of an effective turnaround work scope during the planning phase. Management should be open to making extreme changes to existing work scope criteria. Who is responsible for what and when must also be determined early. In addition, each department must confirm their desire and ability to perform all tasks in the work scope.
Although there is no one size fits all template to creating an effective work scope strategy, good ones include a healthy mix of the following:
- All departments have contributed ideas for increasing effectiveness in the turnaround
- Allowability for changes is built into the work scope, without disastrous consequences
- Clear designation of contractor roles
- Contingency plans for likely and unlikely setbacks
- Commitment of each department to strict but reasonable deadlines
- Work scope management must align with plant objectives
In addition, the support of experienced contractors is crucial to a successful turnaround work scope. A primary role may be assigned to them, and they may contract others to assist them. Regardless, selecting skilled professionals is key to ensuring optimal results from your turnaround. With some turnarounds costing millions of dollars per day, this is not the time to experiment with a contractor that cannot produce a proven track record of successfully completed projects.
A Proven Partner
AMACS provides a full range of process column, tower and vessel internals for many industries including energy, refining, water treatment, and more. Our Houston, Texas manufacturing location produces custom finished mist eliminators, coalescer elements, fractionation trays, column packing (structured, random and grid types), tray hardware, element housings, liquid distributors, wedge wire screens, packed bed supports, limiters and many other specialty process and column internals. We frequently manufacture custom internals, including replacement trays and packing, in days not weeks. For over 70 years, our quick response and plant turnaround support has been a major assistance to our industrial customers who often discover their exact product needs during time critical process upsets or during unit turnaround outages. We can evaluate your process equipment requirements with a quick phone call and then advise the best action plan to meet your time schedule.
Talk to Us
We invite you to call or e-mail your process requirements. Our engineers will thoroughly review your process and offer a design solution or further guidance for your specific process – during or prior to your next turnaround.