How Cost-Effective Modifications can Improve the Performance of Tower Internals
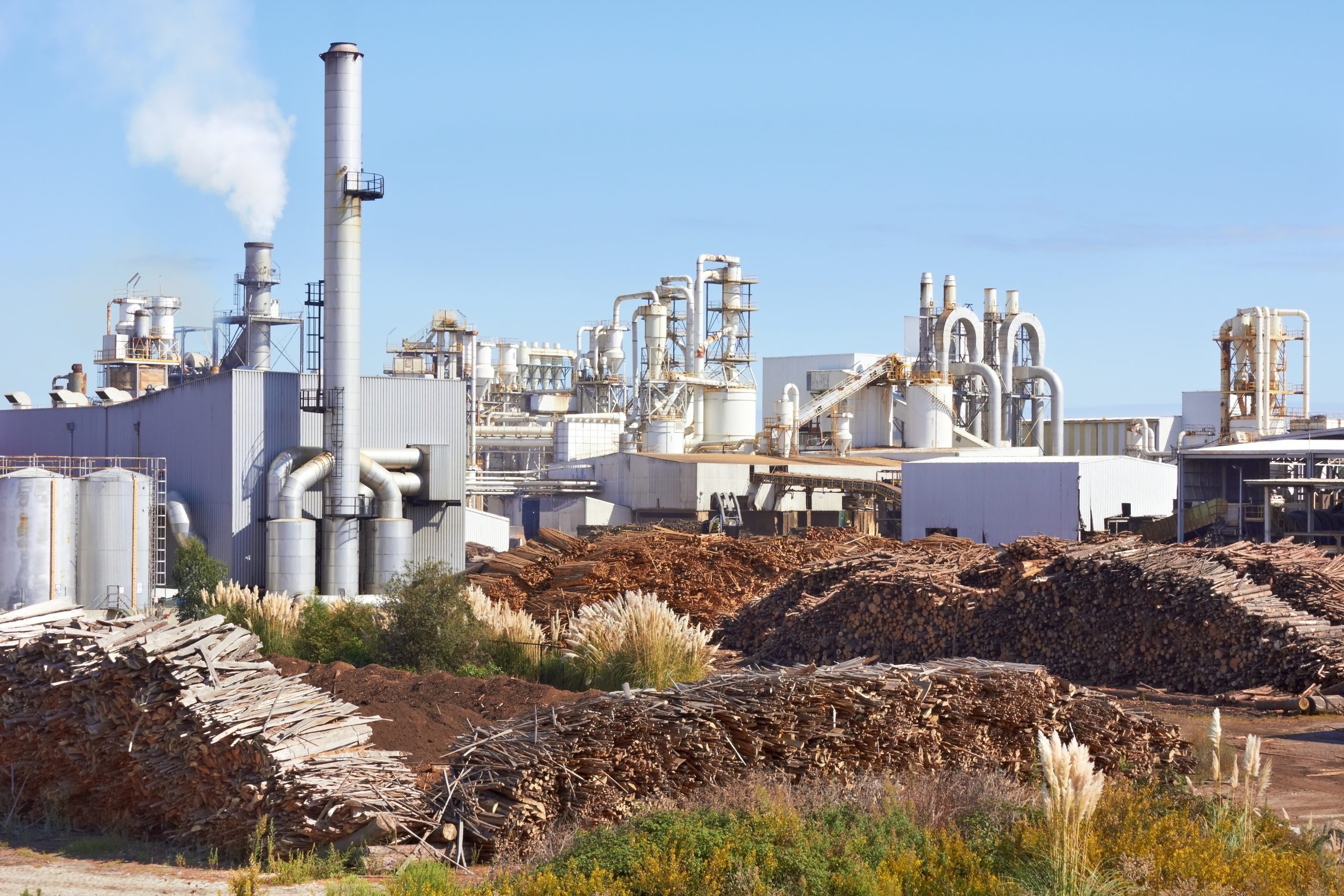
Tower internal operators are constantly on the lookout for high return and low-cost opportunities to increase capacity and reliability without large-scale engineering or investments. A great deal of these opportunities may be discovered during normal maintenance planning and execution, specifically by upgrading tower internals rather than just replacing them. Below we will show you how cost-effective modifications can improve the performance of tower internals.
The Benefits of Modifying Tower Internals
Distillation columns are a large consumer of energy and other resources. As a result, it makes sense to spend the time and money to increase their reliability and efficiency whenever possible. Our own Antonia Garcia is a mass transfer business development manager and has found that to be the case. For example, he found that once a process is in effect, the energy consumption can be higher than originally quoted. One of the best ways to combat this is to improve the mass-transfer performance, especially when a bottleneck is identified. This issue is often caused by mechanical issues or fouling, both of which can be fixed with the correct modifications to the internals.
In one case study, an operator replaced tower internals to improve diesel recovery and achieve flow increases of 15%. As an added benefit, the modifications to the distillation column were able to be done during normal maintenance. The wash section and stripping were modified with specialty trays in a new design. The new trays improved the vapor/liquid interaction as well as increased capacity. As a result of the new improved flow rates in the wash zones, efficiency was increased 12.5% per tray. This was almost double the pre-existing tray configuration.
The Costs of Modifying Tower Internals
As shown above, the time needed to modify the tower internals was minimal. No shutdown or even slowdown was required. And this isn’t unusual. Many modifications can be done during normal maintenance. Those that can’t can also be done in a relatively quick time. However, the cost of downtime should be taken into consideration when calculating the cost in these cases.
Another cost associated with modifying tower internals is the contractors to take on the design. Be sure to get someone who is experienced in both tower internals, as well as your specific process and goals. They should have a consistent track record in your industry for proven success. Finally, there is also the cost of the new tower internals themselves – whether they be trays, packing, wedges, or another configuration.
However, you should consider that many tower internal revamps can be completed as standalone projects at the plant level and can take as little as six months to pay for themselves in improved performance.
AMACS Can Help with Modifications to Improve the Performance of Tower Internals
Our team has the experience to help your operation improve the performance of your tower internals via our selection and expertise in trays, packing, and much more. AMACS will help you choose the correct type for your process while preventing improper internal design from costing you both time and money. Contact AMACS today for more.