4 Tips to Optimize the Efficiency and Reliability of Your Process Columns
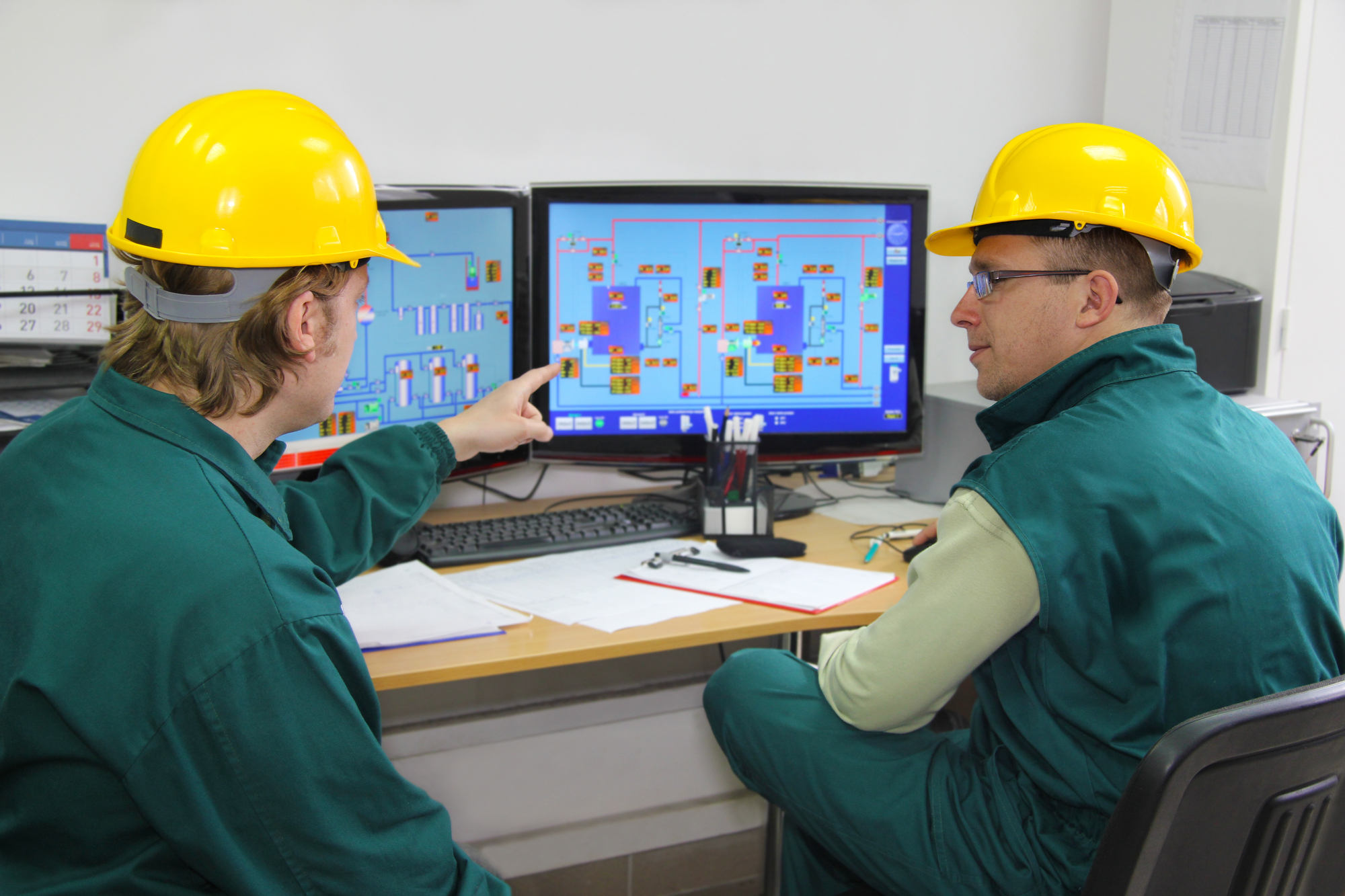
Economic and environmental pressures are pushing managers and operators to look for strategies that will help them achieve increased output from existing columns while experiencing a reduction in energy use. Many turn to the latest and greatest advancements to increase their tower’s performance. But is the latest tech worth the price tag? Below we will share 4 tips to optimize the efficiency and reliability of your process columns to yield the greatest benefit.
- Look at the Entire System
Think of improving your tower’s performance like improving your health. You would start with blood work to see if any of your numbers are too high or low. If you do find numbers outside intended parameters, further tests may be needed. These can include checks for bottlenecks, inefficiencies, and even shutdowns. Another added benefit to checking the system is if you do find an issue that can increase efficiency you may also reduce the risk of breakdowns, cost of fixing equipment, and risk of lost production.
- Consider Replacing Trays and/or Packings
Amazing advancements in trays and packings have been made in just the past few years that can truly optimize the efficiency and reliability of your process columns. Many strategies exist from random packing replacement to installing new, high performance packing. There are even new methods for blending packing in different sizes to get the benefits of both. This includes a packing strategy that combines the efficiency that comes with small packing along with the pressure drop and retainment of capacity in larger packing. For example, this strategy can be beneficial for process columns in fine chemical distillation, smaller refinery towers, retrofit projects, as well as stripping and absorption.
- Design for Specifications
You may experience issues with your process column such as foaming or fouling. There are solutions that can help you avoid these scenarios while improving efficiency. For example, fouling is a common issue in columns. As a result, foul-resistant trays, packings, and even valves have been designed to deal with it. They are designed to provide high-performance in fouling distillation applications. In some situations, a severe service grid packing can result in lower pressure drop and longer run life in applications with severe fouling.
- Be Aware of The Entire Tower
Many towers tend to run inefficiently because they were initially designed for another process. While many of these towers can be successfully modified, others cannot. Process towers designed for certain conditions may not perform well in others because the internals are not suitable for the new process. It can occur in any area from the liquid distributors to the gas distribution setup. It is essential to partner with an experienced contractor with extensive experience in selecting internals for towers in applications just like yours in order to reap the maximum benefits for your budget.
More Tips to Optimize the Efficiency and Reliability of Your Process Columns
For over 70 years, AMACS has been a leading provider of separation and mass transfer technologies to the refining, petrochem, chemical and gas processing industries. Our team has the expertise you need to improve the efficiency and throughput of your process columns, including 24/7 emergency support. Contact us to discuss how we can help!