Planning for Turnaround Success, Part 2: Safety
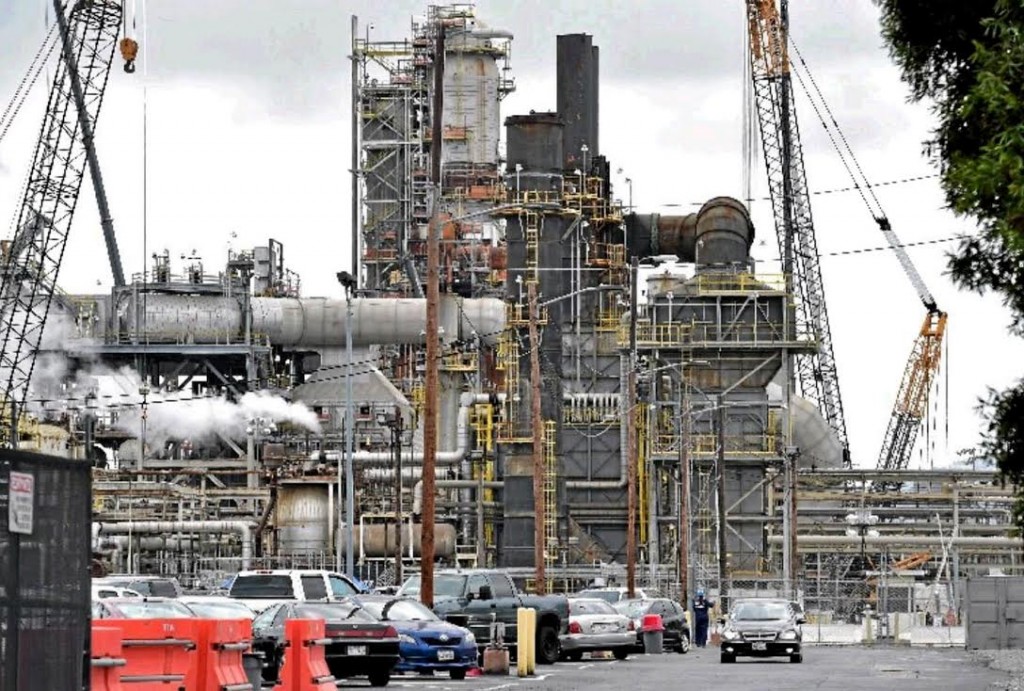
We have previously discussed the crucial steps in planning for turnaround success. In part two of our discussion, we will focus on the most important aspect of planning: safety. One of the best ways to accomplish a successful plant turnaround is to allow enough time to plan the outage correctly and effectively. While each industry has its own standard, a good period for planning is four months prior to the turnaround. Safety is key in the planning phase, as an unsafe turnaround can cause more problems than it solves and leave managers with a price tag far higher than budgeted. Each operation is different, but some of the top considerations include the following.
- Traffic Control
Unnecessary workers and other personnel can’t be injured in the turnaround if they are not allowed into its designated areas. These areas include where work is currently being performed, future work areas and areas where finished work has yet to be inspected and cleared. There are many strategies for controlling traffic during a shutdown, and here are a few:
- Posting clear signage in all limited access areas.
- Providing effective communication as to whom can enter these areas via color codes, schedule, etc.
- Patrolling these areas in the case of a large workforce.
- Maintaining a record and system for who should be where and when.
- Creating an ID or key system that allows or disallows access to certain areas.
- Maintaining an up to the minute list of who is in the plant and exactly where their work is located.
If the limited access areas change, it is necessary to do the above all over again.
- Excess Debris Management
Turnarounds often produce an excess of debris, trash, etc. Anticipate and plan for this scenario by having equipment for cleaning and handling available. In addition to keeping the work area clean, it will also reduce the incidence of slip and falls in the case of liquid or solid debris.
A spill or tear in lines can also cause excessive liquid spill, which is disastrous in the case of hazardous liquids. However, even water can be dangerous when spilled. It can damage equipment, come into contact with electrical currents, and cause many other issues. It is still critical to have protocol in place for spill control and containment, should it occur.
- Proper Safety Equipment On-Hand
It is essential to know what type of equipment is needed for the turnaround and to provide it. Some of this equipment includes:
- Safety shoes with anti-slip protection
- Safety boots with chemical resistance
- Gloves that properly protect against the substance(s) being addressed during the turnaround
- Hard hats
- Eye protectors
- Welding goggles or masks
- Masks to protect from airborne toxins
- Full body suits
Another safety issue in turnarounds is excessive noise. This can include welding, concrete destruction, metal grinding, drilling, sanding, jackhammers, etc. In small doses, these noises can be harmless. If workers are exposed to excessive noise for lengthened periods of time, it can cause hearing damage. Ear plugs, muffs, and other guards are necessary even for workers or visitors who are just in earshot of the work.
In addition, your machines and equipment must be protected. Be sure to have the proper equipment for your systems during the turnaround to prevent exposure, drops, and other forms of damage.
- Use Alarms and Monitors
Many forms of hazardous materials can be inadvertently released without anyone noticing. Using alarms and monitors in areas where these materials are held can prevent them from doing any damage. Specialty alarms and monitors are available to detect gasses like carbon monoxide, benzene compounds, VOCs, and more. There are even oxygen detectors that can help prevent fires. Other monitors can detect leaks by showing a discharge in lines and equipment via motion sensor.
Another monitor worth considering is for machine health. Your equipment will no doubt be affected by the turnaround. These devices can monitor the health of these machines and give detailed reports on items such as vibration, operating temperature, power usage, and run time.
- Provide Safety Training
Whether your operation is small with a handful of employees or a multi-state plant with thousands of workers, external and voluntary safety reviews are essential. Plant safety should be reviewed each year, given the high level of risk that comes with the work. In addition to having emergency procedures in place, you may also consider taking an external safety course. Many providers offer a variety that focus on different industries, materials, and more.
Although AMACS is not a turnaround management contractor, we have long standing relationships with contractors that have been managing turnarounds for years. We are leading providers of tower internals, which are an integral part of most turnarounds. We replace any internal “in kind” on a turnkey basis. With over 70 years of experience, the AMACS Turnaround Team is ready to partner with you! Contact us so we can share in more detail how our Turnaround Team can provide you with all your tower internal needs.