4 Top Challenges in Oil & Gas Turnarounds
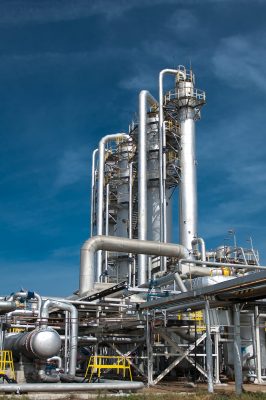
Turnarounds typically involve performing difficult, new tasks such as surface stripping, cutting, welding, draining, moving equipment, catalyst loading, removing all sorts of items, and cleaning to proper industry standards. Unexpected challenges can arise despite the best planning and in all phases of the turnaround. They range from acquiring new equipment to unfamiliarity with a certain process or insufficient planning. The oil and gas industry have their own unique difficulties with turnarounds and these are at the top of the list:
- Not Educating the Right People With the Right Knowledge
A turnaround is complex and brings together workers from all areas with contractors, inspectors, owners, and more. They must perform a series of complex tasks under strict deadlines. Even personnel who have been through oil and gas turnarounds in your facility may not be familiar with new procedures and regulations, or have forgotten what they were taught in the past. It is vital to have constant instruction, as well as taking advantage of advancements in digital technology. Training programs are available in many areas and from many contractors.
- Not Addressing Safety Issues
Each turnaround has its own challenges but the oil and gas industry can see the same safety issues arise time and again. A few include:
- Confined entries – Tasks like inspection and clean-out are often performed in small areas such as manholes, shafts, trenches, and tunnels. Each of these can pose a risk involving anything from restricted movement and poor lighting to exposure to harmful chemicals.
- Benzene – Speaking of the above, benzene is commonly used in the industry and can be harmful if a worker is exposed to it. Benzene has been EPA classified as a known human carcinogen with health risks from inhalation and skin contact. An entry prescreening process with a rugged, portable multi-gas monitor can mitigate this issue.
- Work involving heat – Furnaces inside process units may be used for the turnaround. Workers risk heat stress, excessive noise, burns, and more if the temperature should exceed normal. Workers who weld, braze, or solder are also in danger of fire and explosion, as well as leaking flammable gas. A hot work permit is recommend before entry in each shift, along with a protocol for any airborne hazards. In addition, the proper PPE should always be available.
- Not Enough Framework
Framework is crucial to structure information and should be delivered to all necessary project team members and stakeholders. Incorrect framework can result in poor planning followed by lackluster performance tracking. Specialized software such as Primavera and Cleopatra Enterprise can help maintain the correct turnaround framework.
- Not Enough Adaptability
Even the best planned oil and gas turnarounds are subject to unforeseen challenges that can disrupt the aforementioned framework. Address changes as soon as they arrive and change the framework, plans, and any other documentation immediately. Many turnaround issues occur because some personnel are still working off the old documentation instead of the new. Dedicated digital software that analyzes past data can help foresee these mishaps. You should also collect all the current data for use in any future turnarounds.
The team at AMACS are leaders assisting in oil and gas turnarounds by offering process tower internals. These include items such as feed inlet devices, packing, mist eliminators, wedge wire screens, and more. Contact us if you would like to know how we can help in your next turnaround.