What’s New in Distillation Technology?
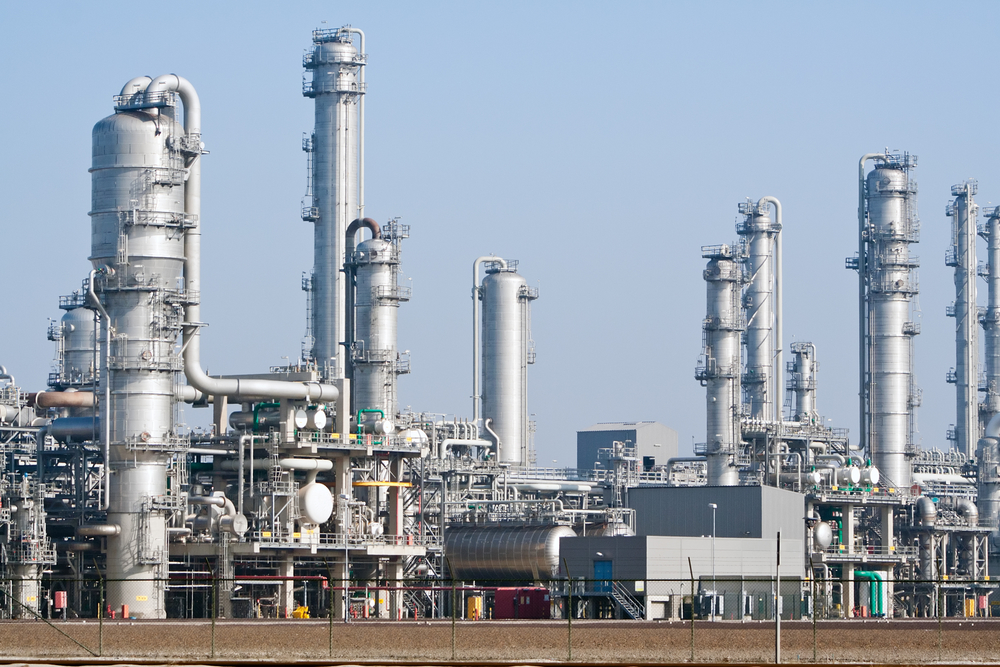
Distillation is a highly used process in our industry renowned for its efficiency, cost effectiveness, and ability to turn trash into treasure. However, industry and regulatory demands are always increasing, as are their requirements for distillation. As a result, there have been many interesting developments in the area of distillation technology.
New Designs in Distillation Column Technology
One of the most important attributes of any tower is its design. New technology has enhanced this in many different ways. For example, electrolyte modeling has been gaining popularity for its ability to predict fouling and corrosive conditions in distillation towers when used with process simulators. They work by determining the acidity and dew point of the first and most corrosive liquid droplets on the column’s metal surfaces. The models made by these electrolyte tools can be accurate in predicting corrosion and fouling, as well as helping to prevent them.
Likewise, many distillation columns are using a dividing wall column, or DWC. It is a column that is self heated and designed to save energy in the column by streamlining three component separations, such as C5, C6, and C7.
New Hybrid Distillation Technology
A hybrid distillation process combines traditional distillation technology with another, newer separation technique or techniques. In these instances, two or more different separation units are combined into a single process. Hybrid separation processes are designed so that one unit overcomes the deficiency of the other. One of the most popular hybrid technologies is where the distillation column is connected to a membrane network for process improvement. Other methods of hybrid distillation technology include combinations of adsorption, crystallization, liquid-liquid extraction, and others.
What’s New in Distillation Column Internals
High capacity packings and trays are increasingly popular in all industries for their ability to improve operations. Packings work with distributors to evenly distribute vapor and liquid throughout the distillation column. Newer packings have been designed for higher capacity, to enhance aerodynamics, reduce drag resistance, as well as provide many other benefits.
In addition, high capacity trays are also improving and offer many options including multiple downcomer trays and truncated downcomer trays. Additionally, there are components that go well with these trays such as push valves, small sieve holes, centrifugal aids, and all sorts of other downcomers. As an example, fouling resistant designs on trays can keep distillation columns in service longer. Truncated downcomer trays increase vapor capacity by using an improved bubbling area. Trays that employ centrifugal separators in the bubbling area can decrease or remove capacity limits caused by jet flood or liquid entrapment.
AMACS has extensive experience in providing and helping you select the best distillation column internals for your operations. We can also help you make sense of what’s new in distillation technology with a focus on optimal performance. Contact us to help you today.