Distillation Improvements: Part 1
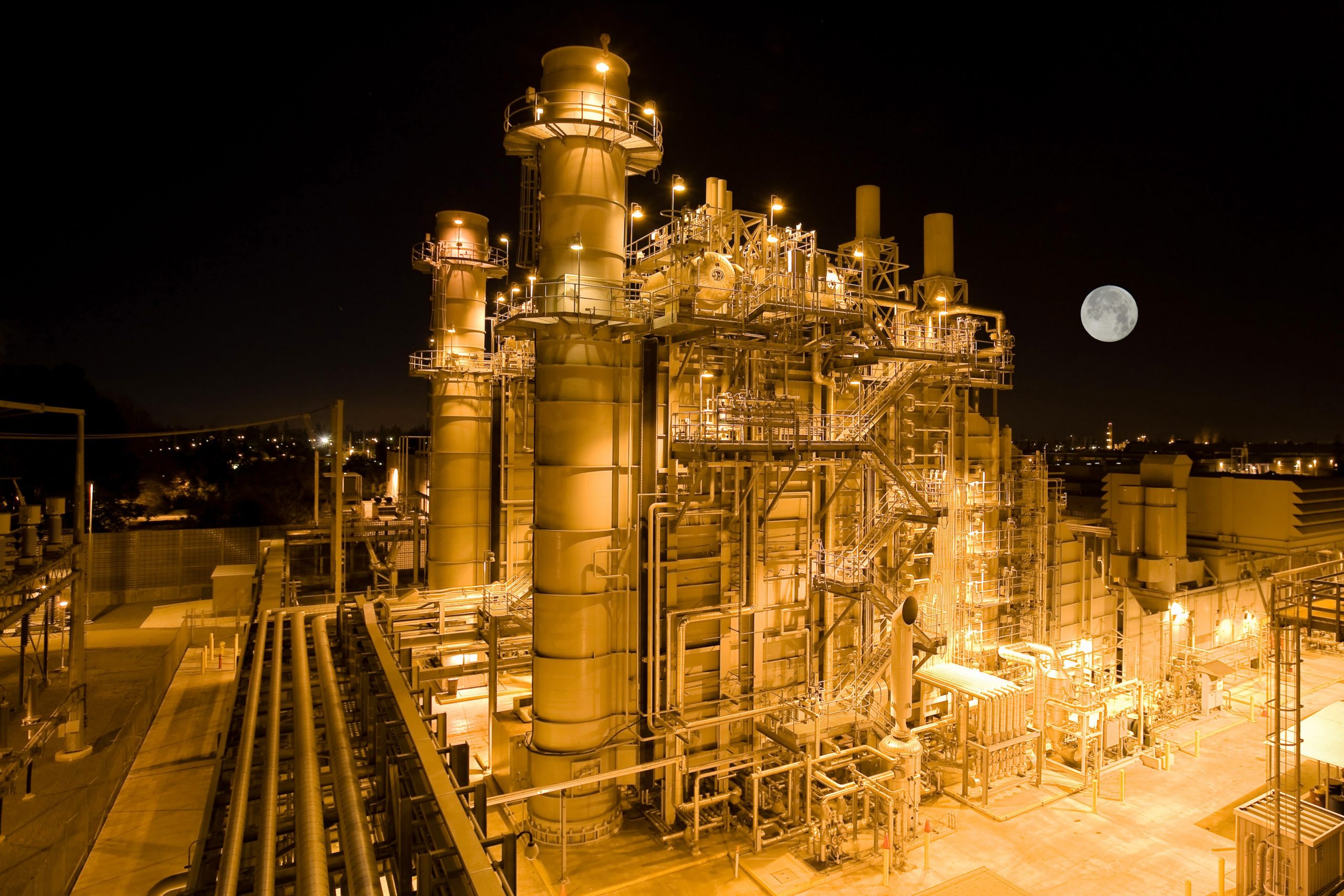
The distillation industry is said to be a stale industry with changes and improvements happening on a rare to occasional basis. While there may be some truth to this sentiment, there are still a few improvements to the technology that have occurred just over the past few years that could improve your towers’ performance.
Controlled Distillation
Distillation control generally focuses on maintaining your products’ purity and recovery. In today’s industry, we must also consider power usage. The new goal is to adjust your column’s controls to avoid overly purifying your product in order to reduce power usage. It is important to control product quality measurement, which can be performed with analyzers. The columns that use analyzers can come with extended sample times but are worth the resulting product.
Hybrid Distillation
This type of distillation includes extractive, azeotropic, and other forms. Hybrid distillation allows you to overcome the limitations of conventional distillation that can decrease energy usage, especially in the case of azeotropic mixtures. Vapor pressure, volatility, attractive and repulsive forces, and other scenarios can benefit from combining two or more distillation procedures. Generally, components are separated via other forms of distillation and use more stages to produce the desired outcome. This can reduce the cost and time it takes to make the desired product.
Dividing Wall Columns
A dividing wall column (DWC) is the use of two or more distillation columns that have been mechanically and thermally joined with a vertical partition to separate the product draw side form the feed zone. This decreases any inefficiencies in mixing found in more traditional types of distillation. Although this is not a recent distillation improvement, it has been perfected over the decades and offers better energy efficiency, with a lower cost, and even a decrease in greenhouse gases.
Distillation Tower Internals
Our personal favorite is the advances in tower internals. In addition to packings and trays, there is also the development of centrifugal motors to separate phases in a quicker manner. For example, there is a new type of random packing that decreases reflux ratios that can consume a lot of energy. It is designed to improve the liquid phase mass transfer coefficient, gas phase mass transfer coefficient, as well as the surface area. Best of all, this packing does not effect hydraulic capacity or pressure drop.
AMACS has extensive experience in distillation improvements and can help you select the right distillation tower internals, as well as other components. There are still more distillation improvements to come, so stay tuned. You may also contact us for help right now.