The Impact of Corrosion in Refineries and Petrochem Plants
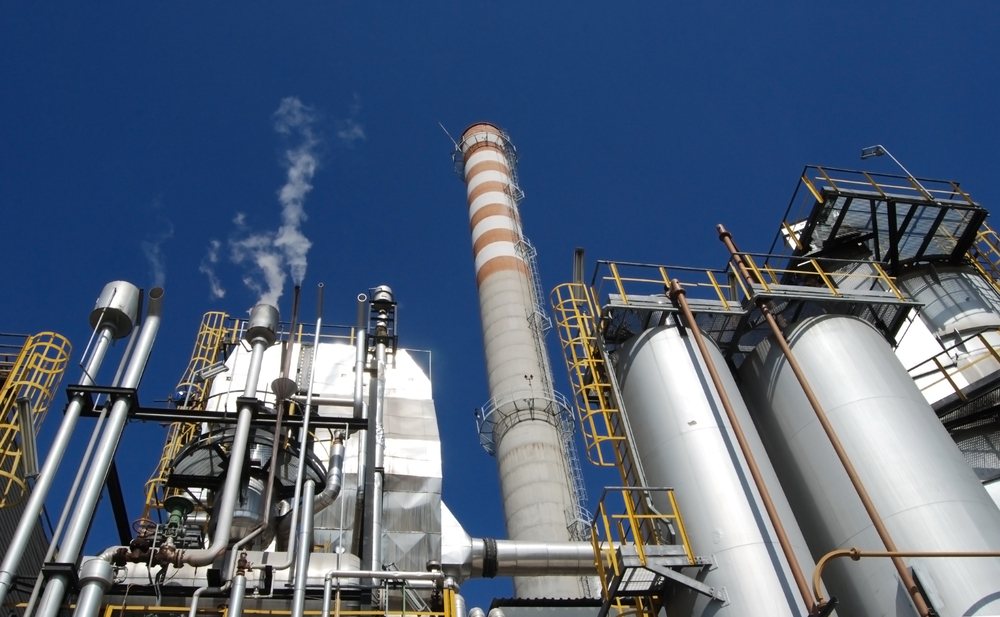
Did you know that corrosion of metals costs the United States economy approximately $300 billion per year according to ASM International? It is estimated that one-third of these losses could be decreased or eliminated through smarter maintenance practices. Below we will help you reduce your impact of corrosion in refineries and petrochem plants.
Types of Corrosion in Refineries and Petrochem Plants
There are two main types of corrosion that occur in refineries: high-temperature corrosion and low-temperature corrosion. High-temperature corrosion is typically caused by water and other condensates that form when equipment is not in use, when it is purged with water or steam, or when it restarts. Low-temperature corrosion is often caused by sour crudes, which become more corrosive as the sulfur content increases. Carbon dioxide is another important corrosive agent in gas operations. Saltwater can also cause corrosion, especially if it is not removed immediately. If saltwater is not removed quickly, hydrochloric acid can form.
The Results of Corrosion in Refineries and Petrochem Plants
Corrosion can be hazardous whether it occurs in crucial or non-crucial equipment. In non-crucial equipment it can lead to equipment failure, damage to surrounding assets, and shutdown of production. In crucial equipment it can lead to intense damage to pipelines, boilers, turbines, and all sorts of other equipment that can cause safety hazards to workers and even the surrounding communities. Typical corrosion can be easily viewed by the eyes, ears, and even nose. However, some forms of corrosion occur internally and are more difficult to stop. Corrosion can occur for any number of reasons such as overuse of equipment, higher or lower than intended operating temperatures, and the transportation of corrosive materials. In fact, over 75% of equipment failures are estimated to be from operating outside intended boundaries. A few examples of equipment that is is more subject to corrosion includes furnaces, crude heaters, heat exchangers, and transfer lines.
How to Prevent Corrosion in Refineries and Petrochem Plants
Five general strategies must be studied and correctly implemented in order to decrease corrosion:
- Coatings – Many plants already have equipment in place and can’t select materials to combat corrosion. However, many coatings are available to help protect equipment. These are made for either metallic or nonmetallic equipment. Metallic coatings are used on top of existing metal to protect equipment such as tin-plating or galvanized steel. Non-metallic coatings isolate the metal from any corrosive exposure.
- Material selection – When selecting a new piece of equipment, machine, or even component for your petrochem plant it is vital to ensure it is made of anti-corrosive materials like allows specifically made for your application, such as stainless steel, high nickel alloys, INCONEL, MONEL, and similar materials.
- Inhibitors – A few examples of corrosion inhibitors include chromates, silicates, and organic amines. Inhibitors work best when used in closed systems where you can maintain the inhibitor amount.
- Cathodic protection – This method suppresses corrosion by two methods: impressed-current systems or sacrificial-anode systems that are applied based on the material and type of corrosion protection needed.
- Design – Corrosion most likely happens in dead crevices that can be eliminated or minimized by intelligent design. It may require moving parts and components, but you may anticipate any maintenance or repair issues that may arise.
More on The Impact of Corrosion in Refineries and Petrochem Plants
AMACS is the Gulf Coast’s premier provider of column internals and hardware for refineries and petrochemical plants during turnarounds, shutdowns, and outages (TSO). We improve the efficiency of many situations with our advanced packings, trays, and other internals. Contact the AMACS team to discuss how we can help you during your next turnaround or shutdown.