Choosing Tower Internals for LNG
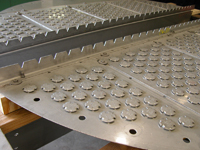
Previously, we wrote a Quick Guide to Selecting Tower Internals and now we want to expand on that idea. The type of tower internal depends greatly on the type of media you are working with such as shale, crude oil, etc. Today we will be discussing how to choose your tower internals for LNG (liquefied natural gas) and FLNG (floating liquefied natural gas).
Intro to Tower Internals for LNG
One of the best ways to go when choosing LNG tower internals is to use an absorber that contains structured or random packing to reduce the levels of CO2 sufficiently for gas liquefaction. This level is usually 50 ppmv (parts per million volume). The packing is made from various sizes and can use trays that affect absorber performance. Packing that is too large results in failure to achieve the treating goal. Packing that is too small will cost more due to higher packing and is also more susceptible to plugging while reducing the capacity of the tower. You must also select the right options for FLNG, due to its severe weight and footprint restrictions, which comes with a need for increased accuracy and reliability.
LNG Packing Versus Trays
There is a test case involving the revamp of an LNG plant using GAS/SPEC 2020 solvent to treat a feed gas with 2.24% CO2 at about 4 MPa. Trayed columns were used but were unable to reach over 70% of the nameplate capacity due to foaming. Both towers were replaced with others that had somewhat larger diameter, and trays were replaced with structured packing. The packing was provided by a local manufacturer and appeared similar to well-known commercial brands. In the end, the results were favorable for their operation.
In short, packing is preferable to trays for LNG for many reasons including but not limited to:
- Increased tower capacity
- Decreased pressure drop
- Reduction of foaming issues
- Higher selectivity
- Better resistance to rocking motions in towers
Benefits of Structured Packing for LNG
Structured packings are preferable for LNG because they have a great deal of flexibility in treatment which allows them to be used where trays are very difficult to apply. This is due to their wide range in sizes and their laterally compartmentalized flows. However, using structured packing can be difficult because not many contractors have experience with it, and it can be difficult to translate the calculations to real world tower internals. We recommend choosing your tower internals first and foremost with a contractor with experience in the field who can tell you the mass transfer rate before you make a decision.
Let AMACS be your partner in providing the correct LNG and FLNG replacement-in-kind trays, packing, and other internals for your columns. We are a reliable source for the knowledge you need when selecting internals for existing and new towers. Our team offers consistent, quick delivery for tower internals in many commonly stocked alloys and diameters.