4 Tips for Overcoming Backlogs in Maintenance Tasks
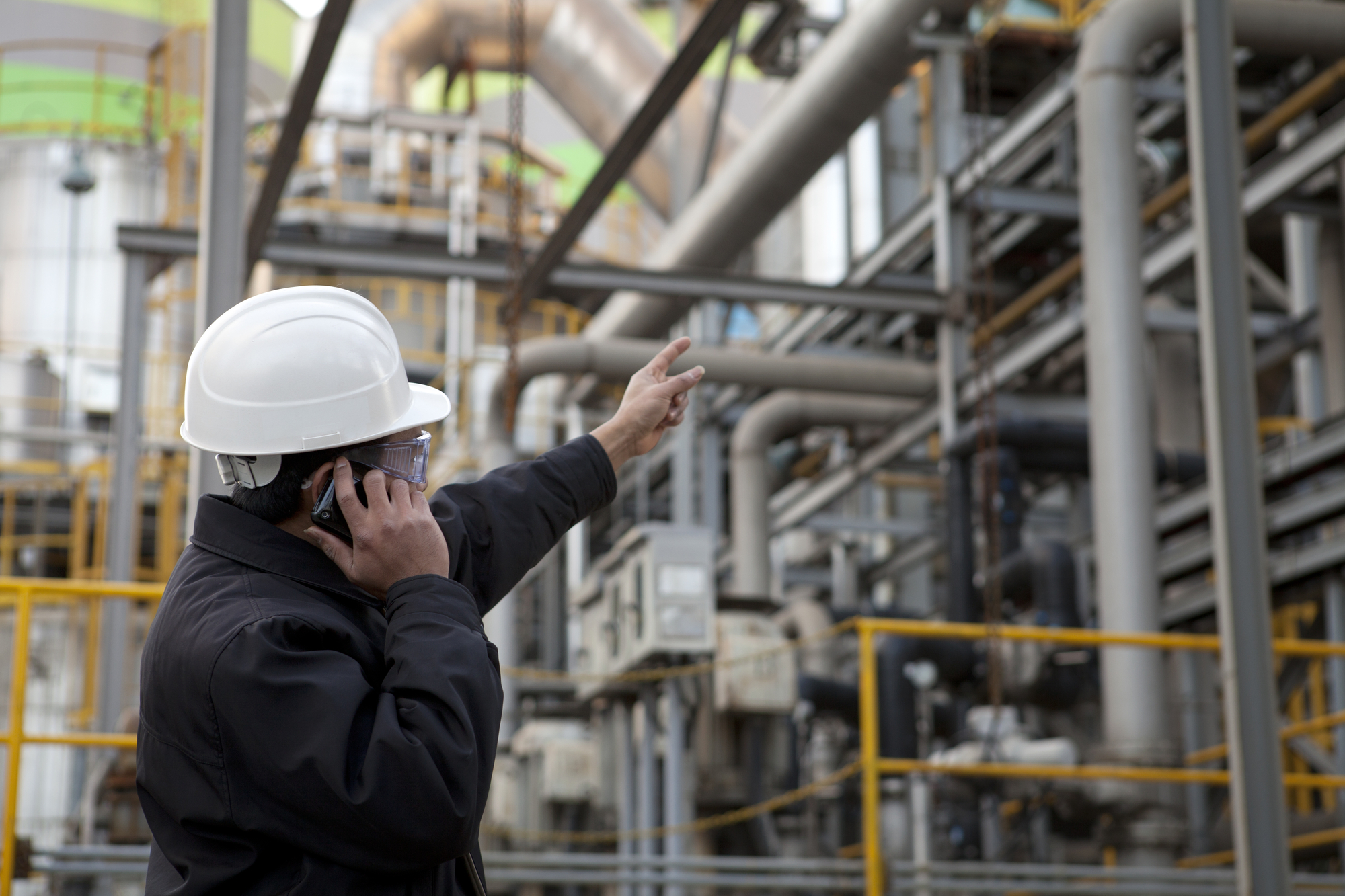
Facilities across the world continue to grapple with higher demands coupled with limited resources, supplies, and a sluggish supply chain. This all leads to an ever-growing issue of expanding backlog items. It can result in poor customer experience that comes from the frustration of critical needs being placed on hold rather than in active development. Project managers must come up with a priority list, roadmaps to achieving these goals, and specifications of what is needed and when – not to mention dealing with the challenges of constantly-moving goal posts. Below, we will help you meet your goals with these 4 tips for overcoming backlogs in maintenance tasks.
- Determine what is causing your backlog
Backlogs generally occur for three reasons: 1. Unclear actions such as performance maintenance, buying new equipment, replenishing inventory, etc. You should know what maintenance needs to be performed on what, what new equipment you need, how much inventory you need versus what you can get. 2. Too many details. On the other hand, you may suffer from too many details such as who needs to perform maintenance. Be flexible on details when possible. 3. Lack of ownership. Your team may know exactly what needs to be done, but no one feels in charge. Be clear about who is in charge of what and when it will be completed, including your own items.
- Prioritize the Backlog
Once you have identified what you need to do, you can’t do everything at once. For example, you may shift maintenance workloads into items such as urgent, critical, and as needed in order to keep work execution manageable. A risk matrix can also be useful and can be done by asking questions such as:
- How urgent is this work?
- What is its impact on safety, performance, uptime, etc?
- What is the cost of this work in both funds and time?
- What is the cost of delaying this work?
- Do I have the materials/contractors/permits/etc for the work ready?
- Designate Tasks and Owners
It is essential you designate tasks to project managers in order to get things done when overseeing a backlog. If not, crucial items like timeline and budget will fall through the cracks and affect other projects. Assigning a project owner creates a concrete strategy for each backlogged project and is more likely to ensure goals and deliverables are done on time and on budget.
- Collect Data
Don’t miss the opportunity to collect all appropriate data on each project, challenges, successful strategies, and more. New technology makes this easier than ever and can let you compare data across time. Plant owners or asset operators should keep track of best practices for predictive, preventative, and material management tactics to ensure continued success on future projects.
You may also create or improve on a uniform tagging guide for naming, numbering, and descriptions on all equipment and machinery. Utilize the existing foundation or build a new one in your CMMS/ EAM system to increase the efficiency and quality of maintenance work.
More Tips for Overcoming Backlogs in Maintenance Tasks
AMACS is the Gulf Coast’s leader in providing process tower internals and services for turnarounds, shutdowns and outages. We improve the reliability and performance of process towers by offering the latest in packings, trays, and other internals for various applications. Contact us to discuss how we can help with your backlog in maintenance tasks.