Effective Team Organization for Turnaround Success
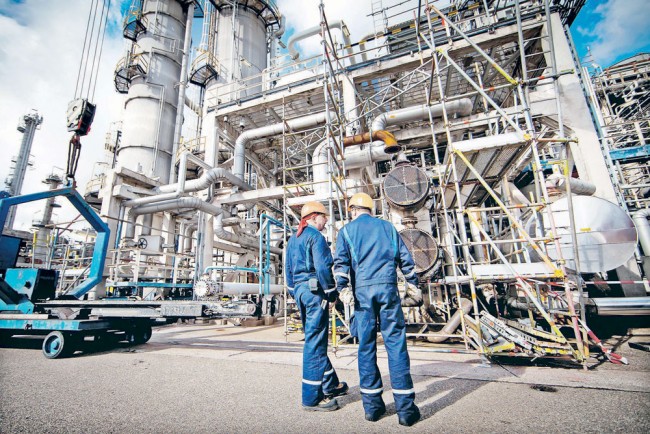
In the fast-paced and high-pressure environment of a plant turnaround, the success of the operation hinges not just on technical expertise but on the ability to assemble and manage an efficient, cohesive team. A well-organized turnaround team is a critical factor in completing the project on time, within budget, and to the highest safety and quality standards. The right mix of personnel, from internal staff to external contractors, must work together seamlessly to navigate the complexities of a plant shutdown, equipment overhaul, and restart. Below are key considerations and strategies for organizing your turnaround team to maximize efficiency and minimize risk.
- Designate a Turnaround Leader
While ownership and senior management may set the agenda for the turnaround, it’s essential to appoint a point person or a team of key leaders to manage the day-to-day logistics and decision-making. This person or team is responsible for ensuring that the turnaround plan is executed smoothly and that all stakeholders remain aligned throughout the process.
The turnaround leader should be someone with a proven track record in managing complex, high-stakes projects, particularly in plant environments. Critical traits to look for include:
- Crisis Management Skills: Turnarounds inevitably come with challenges, unforeseen complications, and emergency scenarios. The leader must remain calm under pressure and have the ability to make swift, effective decisions.
- Leadership and Accountability: This person must inspire confidence, hold team members accountable, and drive the turnaround to completion.
- Cross-Departmental Coordination: A turnaround requires input from multiple departments—operations, engineering, safety, HR, procurement, and more. The turnaround leader must facilitate communication and collaboration across these departments.
- Selecting Key Team Members
When assembling your internal turnaround team, consider the specific areas of expertise needed to navigate each stage of the turnaround process. Rather than selecting individuals with overlapping skill sets, focus on building a diverse team whose strengths complement one another. An effective team will include personnel from core functions such as:
- Project Management: A strong project management team ensures milestones are met and the schedule stays on track.
- Engineering and Operations: These individuals should have a deep understanding of the plant’s technical systems, as they will be directly responsible for equipment inspections, repairs, and system upgrades.
- Procurement and Logistics: These team members ensure that the necessary materials and parts are available and delivered on time to avoid delays.
- Safety and Compliance Officers: Turnarounds are high-risk operations, so safety should be a top priority. A dedicated safety team will enforce best practices and ensure compliance with industry regulations.
To select the best candidates for your turnaround team, create a detailed organizational chart that includes the following information for each key member:
- Current Roles and Responsibilities
- Relevant Experience and Achievements
- Strengths and Areas for Development
- Past Success in Similar Projects
- Ability to Meet Critical Timelines
- Accountability and Problem-Solving Skills
- Integrating External Experts
While your internal team will handle many aspects of the turnaround, there will be times when you need specialized knowledge or additional manpower. External experts are critical to the success of the turnaround, and careful selection is essential.
Key external team members may include:
- Financial Experts: Having a financial team on board is crucial to ensure that the turnaround is completed within budget. They help forecast costs, track expenses, and make adjustments when necessary to avoid budget overruns.
- Legal Counsel: Legal experts specializing in turnarounds can provide valuable insight into liability concerns, regulatory compliance, and contracts with vendors or contractors. They also help protect your organization from legal risks associated with workplace accidents, safety violations, or contract disputes.
- Inspection and Certification Teams: Depending on the nature of the turnaround, inspectors may be needed to ensure compliance with industry standards and government regulations. This could include pressure vessel inspections, electrical system checks, or safety audits.
- Specialized Contractors: Many turnarounds require contractors with expertise in specific tasks, such as welding, scaffolding, or complex equipment installations. Carefully vet these contractors to ensure they align with your organizational values and safety culture.
A major factor in the success of external contractors is ensuring that they operate with the same high standards as your internal team. Evaluate their track record in completing turnarounds on schedule and within budget. Regularly monitor their progress and maintain clear communication to avoid surprises.
- Develop a Comprehensive Master Document
One of the most important tools for managing a successful turnaround is the master document, which serves as the central repository for all turnaround-related information. This document should be updated regularly throughout the project and accessible to all key stakeholders.
The master document should include:
- Timeline and Milestones: A detailed schedule of tasks, deadlines, and key milestones that must be met throughout the turnaround process.
- Task Assignments: Clear allocation of responsibilities for each team member, both internal and external.
- Budget Tracking: A real-time breakdown of expenses, including material costs, labor, contractor fees, and contingencies.
- Safety and Compliance Checklist: Detailed safety protocols and compliance requirements that must be followed.
- Risk Management Plan: Identification of potential risks, along with strategies for mitigation and contingency planning.
This document serves as the project’s “bible,” helping to keep everyone on track and accountable.
- Responding to Challenges and Change
Despite the best-laid plans, issues will arise during the turnaround. Having a flexible team that can pivot when necessary is crucial to overcoming obstacles without compromising the turnaround timeline or quality.
If external factors such as regulatory changes, unforeseen mechanical failures, or labor shortages arise, your turnaround team should be able to adapt quickly and efficiently. Encouraging open communication and a problem-solving mindset across all departments will ensure that the team can respond proactively to challenges.
The Key to a Successful Turnaround
At AMACS, we understand the complexity and demands of managing a successful process plant turnaround. With over 40 years of experience in providing advanced separation and phase contacting internals for the oil and gas, refining, chemical processing, and other industries, we’ve helped customers complete turnarounds on time and within budget, ensuring optimal performance post-restart.
By assembling a well-rounded, highly-skilled turnaround team—both internal and external—and maintaining a disciplined approach to planning and communication, you can dramatically increase the likelihood of a successful turnaround. For more information about how AMACS can support your next turnaround with reliable, high-quality process internals, contact us today. Let us help you streamline your turnaround process and meet all of your plant’s operational needs.