10 Critical Steps to Ensure a Successful Turnaround
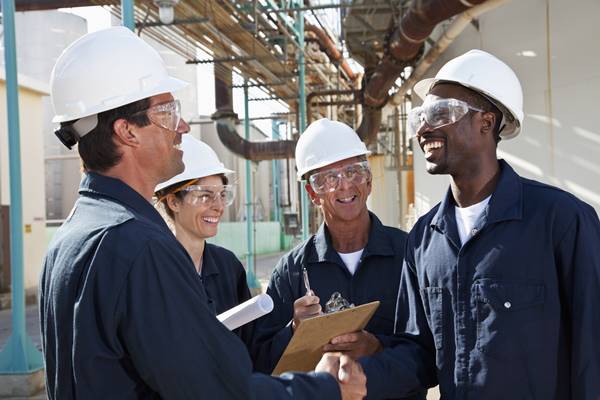
A plant turnaround — also known as a planned shutdown or outage — represents one of the most complex, costly, and resource-intensive events in the operational lifecycle of a facility. For process plants in industries such as refining, petrochemicals, oil & gas, power generation, and chemical manufacturing, a turnaround is not merely a maintenance window — it is a strategic event with significant financial and operational impact.
Turnarounds can cost millions of dollars, often equating to the annual maintenance budget of a facility condensed into a matter of weeks. According to industry sources like Maintenance Resources and the Association of Turnaround Industry Professionals (TAP), a large-scale refinery turnaround can easily exceed $100 million in direct and indirect costs. Beyond finances, turnarounds affect supply chains, production targets, client deliverables, and investor expectations.
Given the high stakes, proper planning, execution, and quality control are paramount. At AMACS, we combine decades of expertise with a solutions-driven approach to help clients navigate the complexities of turnarounds. Based on industry best practices and our experience supporting critical projects across the U.S. Gulf Coast and beyond, here are the 10 essential steps to a successful turnaround.
- Strategic Planning: Establishing the Roadmap for Success
Effective turnarounds begin with comprehensive, detailed planning that starts 12-24 months in advance of the shutdown window. This phase defines critical parameters, including:
- Planned start and end dates
- Equipment and systems scheduled for removal, inspection, or replacement
- Maintenance scope: proactive vs. reactive tasks
- Inspection protocols, compliance requirements, and risk assessments
Advanced tools such as Computerized Maintenance Management Systems (CMMS) and 3D plant modeling may be utilized to aid visualization, scheduling, and scenario planning.
- Accurate Budgeting: Balancing Cost with Performance
Industry data suggests that turnaround costs often range from 2-4% of the plant’s total replacement value (TRV). For facilities valued in the hundreds of millions, this is a substantial investment.
- A realistic budget accounts for:
- Labor costs (internal and contract labor)
- Materials, spare parts, and specialty equipment
- Downtime cost per day/hour
- Contingency reserves (typically 10-20% of the estimated budget)
At AMACS, we support clients by offering cost-effective solutions for internals, separation equipment, and mist elimination systems — ensuring budget optimization without compromising on performance.
- Partner Selection: Leveraging Industry Expertise
Successful turnarounds rely on collaboration with trusted partners who offer specialized expertise in plant operations, process engineering, and fabrication. Selecting a vendor or engineering partner involves evaluating:
- Industry experience
- Safety performance history
- Technical qualifications
- Understanding of your facility’s specific processes
AMACS brings a legacy of excellence in designing and manufacturing process internals and equipment that directly support plant reliability during and after turnaround events.
- Role Assignment and Accountability
Turnaround execution requires clearly defined roles and responsibilities for all personnel, both internal staff and external contractors. Key positions include:
- Turnaround Manager (TAR Manager)
- Discipline Leads (Mechanical, Electrical, Instrumentation)
- QA/QC Supervisors
- Safety Coordinators
Defined reporting structures and daily progress tracking help avoid scope creep and mitigate risks.
- Early Procurement and Material Management
Supply chain disruptions and long lead times can derail turnaround schedules. Critical materials — including replacement parts, trays, mist eliminators, reactor internals, and vessel components — should be ordered well in advance.
AMACS specializes in the fabrication of custom-designed equipment engineered to meet client specifications, reducing the risk of delays caused by generic or ill-fitting components.
- Safe and Systematic Equipment Removal
During the initial phase of physical work, equipment designated for removal or replacement must be safely and efficiently extracted. This includes:
- Column internals
- Heat exchanger bundles
- Mist eliminators
- Catalyst beds or packing media
Proper tagging, documentation, and storage procedures are essential for asset integrity and future reinstallation.
- Inspection and Testing
Inspections during turnarounds provide a rare opportunity to assess equipment conditions that are normally inaccessible. Techniques include:
- Non-Destructive Testing (NDT)
- Visual inspections
- Ultrasonic Thickness Testing (UTT)
- API compliance checks
Data collected from these inspections guide repair versus replacement decisions and inform predictive maintenance programs.
- Repair, Installation, and Maintenance Execution
Repairs and equipment installation must follow the sequence of critical path tasks, with particular focus on:
- Replacement of column and tower internals
- Mist eliminator upgrades for improved throughput
- Heat exchanger cleaning or tube replacement
- Packing replacement or optimization
AMACS provides precision-engineered solutions to enhance process performance, extend equipment life, and reduce future maintenance burdens.
- Quality Assurance and Final Testing
No turnaround is complete without rigorous QA/QC protocols. Testing verifies:
- Proper equipment alignment and fit
- Leak-free reassembly
- Compliance with safety and environmental standards
- Advanced tagging systems and turnover documentation ensure accountability and traceability.
- Restart and Operational Validation
The final step is a carefully controlled plant restart, with performance validation based on:
- Process flow rates
- Pressure and temperature parameters
- Emission control standards
- Post-startup inspections
A successful restart not only restores operations but often improves them through upgraded systems and optimized internals.
Partner with AMACS for Your Next Turnaround
At AMACS, we understand that every turnaround is an opportunity — not just for maintenance, but for performance improvement, reliability gains, and operational excellence.
Our team provides custom-designed process internals, separation equipment, and technical consultation tailored to the unique needs of our clients across refining, chemical, and oil & gas industries.
Whether you require mist eliminators designed for high-efficiency capture, custom tower packing, or engineered internals for challenging applications, AMACS delivers proven solutions on time and within budget.