Understanding the Differences: Shutdowns, Turnarounds, and Outages in Refinery Operations
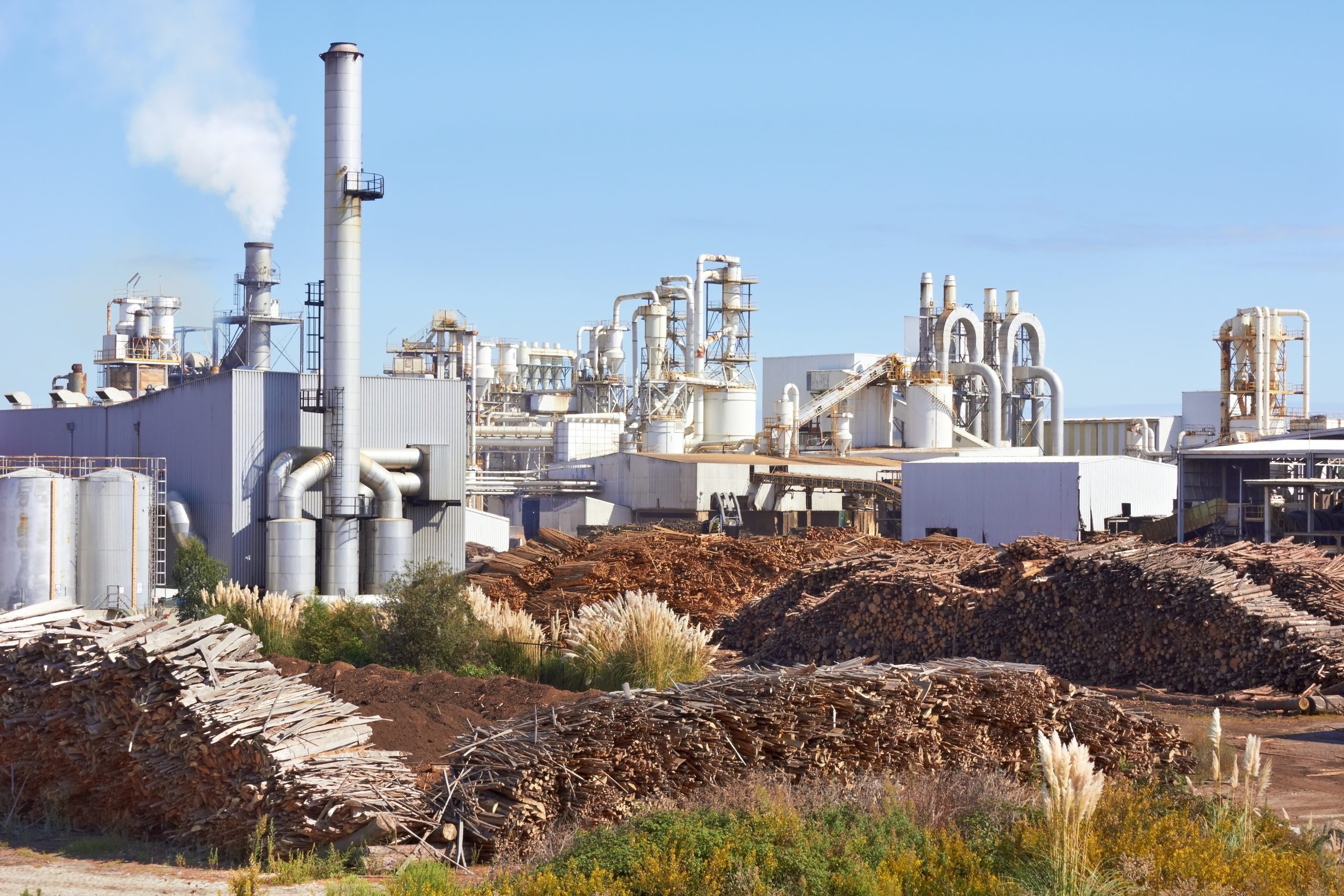
In the refining industry, operational continuity is critical to profitability, safety, and regulatory compliance. Disruptions—whether planned or unplanned—can significantly impact output and bottom lines. Among the most significant operational events are shutdowns, turnarounds, and outages (STOs). While often used interchangeably, these events differ in their causes, predictability, and management strategies. This article breaks down the distinctions and technical implications of each, helping refinery managers improve planning, execution, and recovery.
Turnarounds: Strategic, Scheduled Overhauls
A turnaround is a scheduled and meticulously planned event in which part or all of a refinery is taken offline for comprehensive maintenance, equipment upgrades, inspections, and regulatory compliance work. Turnarounds can involve everything from heat exchanger cleaning to replacing major process internals such as trays, packing, or reactor components. Industry-wide, large-scale turnarounds occur approximately every 3 to 6 years, depending on the unit’s operating conditions and manufacturer guidelines.
According to the American Petroleum Institute (API), refining companies allocate up to $200 million or more per major turnaround, and delays can cost upwards of $1 million per day in lost production. Given this financial weight, effective scope development, pre-turnaround inspections, long lead-time parts procurement, and contingency planning are essential.
Best Practices:
– Use condition-based monitoring and risk-based inspection (RBI) to prioritize asset intervention.
– Leverage digital twin models or simulation software to optimize turnaround planning and clash detection.
– Incorporate real-time updates to manage scope creep and maintain productivity.
Furthermore, post-event evaluation is often overlooked but is critical to improving future performance. Lessons learned from early stages (e.g., turbine overhauls) can be quickly applied to improve efficiency across remaining assets in the same cycle.
Shutdowns: Emergency Response and Rapid Recovery
A shutdown refers to an unscheduled or emergency stoppage of a processing unit or entire facility due to safety concerns, equipment failure, or environmental incidents. Unlike turnarounds, shutdowns are reactive in nature and often unbudgeted. They can arise from compressor failures, corrosion-related leaks, instrumentation malfunction, or incidents such as fires or explosions.
For instance, in 2022, a fire in a Toledo refinery forced an immediate shutdown after a gasoline-producing unit was compromised. Investigations revealed mechanical integrity lapses—underscoring the importance of proactive maintenance strategies.
Emergency Protocols Should Include:
– Immediate personnel accountability and area isolation.
– Root cause analysis (RCA) and event reconstruction to determine failure mechanisms.
– A restart plan including inspection, decontamination, and recommissioning procedures.
Given that unplanned shutdowns can cost refineries millions in downtime, many operators now utilize predictive maintenance analytics and early warning diagnostics to reduce their frequency and severity.
Outages: Power Interruptions and Contingency Planning
Outages, often related to power supply disruption, are another major cause of downtime in refinery operations. These may be caused by grid failures, weather events, or internal equipment issues like transformer failures. Outages can be planned—for infrastructure upgrades—or unplanned, which are more disruptive and risky.
A planned outage typically aligns with larger project work and includes coordination with utility providers, backup power sources, and temporary operational shifts. An unplanned outage, on the other hand, requires immediate engagement of backup systems such as diesel generators or battery-powered instrumentation for critical systems.
Key Considerations:
– Install uninterruptible power systems (UPS) for control rooms and emergency instrumentation.
– Maintain critical spare parts for switchgear and transformers.
– Develop black-start protocols to restore systems without relying on the grid.
According to the U.S. Energy Information Administration (EIA), power interruptions in industrial sectors account for billions in annual losses, with the refining sector being one of the most sensitive due to the continuous nature of operations.
AMACS: Your Partner for Reliable Turnaround and Shutdown Support
At AMACS, we understand the high stakes of shutdowns, turnarounds, and outages. That’s why we support refineries with precision-engineered mass transfer and separation internals, helping optimize process performance during both planned maintenance and emergency recovery. Our team collaborates closely with plant personnel to ensure that replacement internals—such as trays, structured packing, and mist eliminators—are fabricated and delivered on time, reducing costly delays.
Whether your refinery is preparing for a long-term turnaround or recovering from a sudden outage, AMACS delivers the components and expertise you need to minimize downtime and maintain operational excellence.