7 Technical Strategies to Maximize Efficiency and Reliability in Process Columns
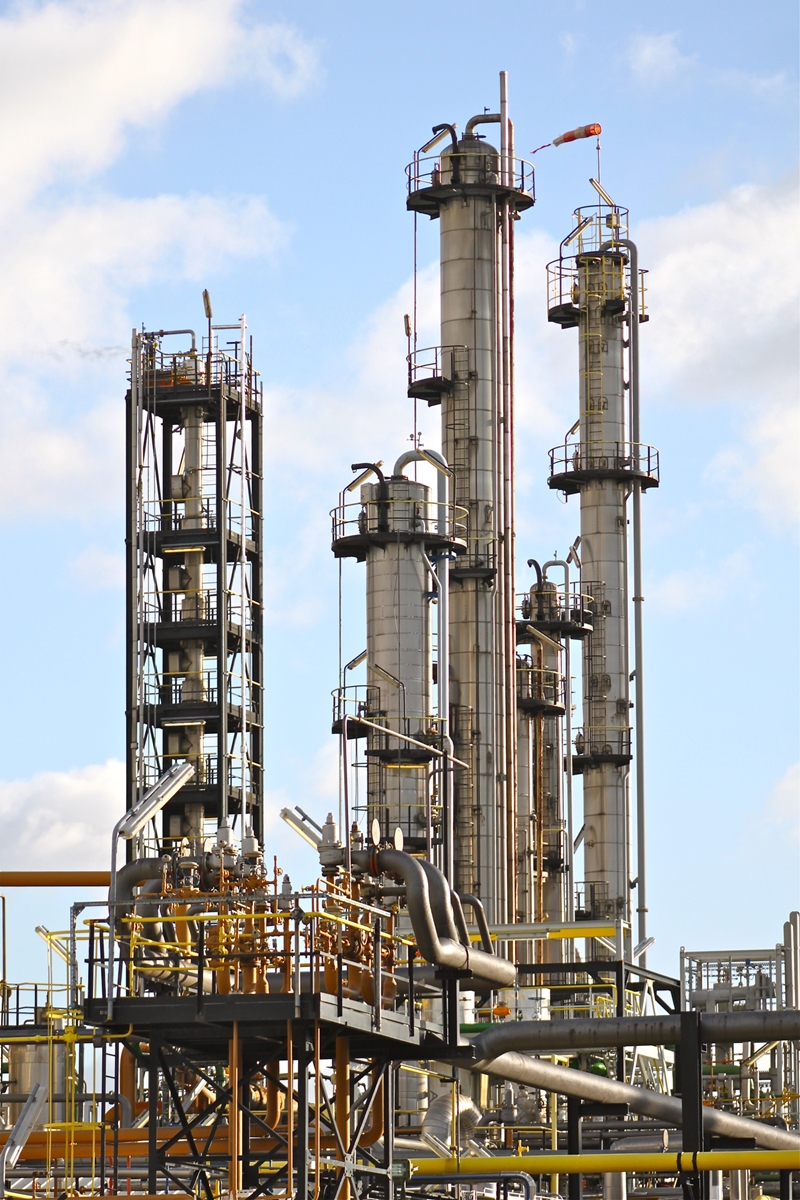
With increasing demands for sustainability and profitability, plant operators face mounting pressure to extract more performance from existing assets while minimizing energy consumption and downtime. Process columns, particularly in distillation, stripping, and absorption applications, offer opportunities for significant efficiency gains—if approached systematically. Rather than defaulting to the latest (and often costly) innovations, optimizing column performance should start with a full-spectrum evaluation of system behavior, hardware integrity, and operating conditions.
Here are seven proven strategies to enhance the performance and reliability of your process columns:
-
Conduct a Full-System Diagnostic Assessment
Optimizing a process column begins with understanding the system as a whole. This includes evaluating upstream and downstream influences, heat integration, column hydraulics, and pressure profiles. Process simulation tools can be used to model thermodynamic behaviors under various loads and identify imbalances such as vapor-liquid maldistribution, reboiler inefficiencies, or condenser bottlenecks. Infrared thermography, gamma scanning, and other diagnostics may further reveal internal malfunctions like fouled trays or damaged packing. A systems-level audit often identifies both performance bottlenecks and hidden mechanical risks—allowing you to mitigate breakdowns before they affect throughput.
-
Upgrade Column Internals: Trays and Packings
Column internals play a critical role in vapor-liquid contact efficiency. Modern advancements in tray technology—such as high-capacity valve trays or dual-flow trays—offer superior vapor handling and resistance to fouling. Likewise, structured and random packing technologies have evolved significantly. Hybrid systems, which combine small packing in the bottom section (for increased surface area) with larger packing at the top (to reduce pressure drop), can improve mass transfer efficiency without compromising capacity. These configurations are ideal for high-purity separations in fine chemical distillation, retrofit operations, or towers with hydraulic constraints.
-
Evaluate Fouling-Resistant Solutions
Fouling and corrosion can severely degrade column performance over time. In applications prone to polymerization, salt deposition, or particulates, specialized internals designed for severe service are essential. Grid-style structured packing, anti-fouling valve trays, and fouling-tolerant liquid distributors extend service life and reduce cleaning frequency. Choosing metallurgy and mechanical design that withstands corrosive environments—such as high-chloride or sulfur-laden streams—also plays a role in reducing downtime and unplanned outages.
-
Validate Column Design Against Actual Process Conditions
Columns originally designed for one set of conditions are often repurposed over time—sometimes without adequate re-engineering. If a tower is now operating under different feed composition, temperature, or pressure conditions, the original internals may no longer be suitable. Maldistribution, excessive pressure drop, or low tray efficiency are common in such scenarios. A revamp study using updated simulation and hydraulic models can determine whether existing hardware should be modified, upgraded, or replaced entirely to meet new process demands.
-
Optimize Fluid Distribution and Redistribution
Liquid and vapor distribution are critical for maintaining consistent contact across trays or packing surfaces. Poor distribution leads to channeling, weeping, and localized flooding. Installing high-performance redistributors, calming zones, and liquid collectors can improve phase contact and help avoid premature efficiency loss. In packed towers, properly designed redistributors between packing beds restore uniformity, especially in tall columns or systems subject to flow rate variability.
-
Control Pressure Drop and Energy Consumption
Columns with high pressure drop consume more energy and can limit capacity during peak demand. Selecting low-resistance internals—such as structured packing instead of trays or using high-capacity tray valves—can reduce reboiler and overhead fan loads. In vacuum towers, pressure drop minimization becomes especially critical to maintaining product recovery and minimizing energy input. The trade-off between pressure drop and separation efficiency must be evaluated through both hydraulic modeling and pilot testing when applicable.
-
Engage Experienced Tower Specialists
No optimization strategy is complete without expert insight. Working with a contractor that specializes in separation and mass transfer systems ensures that you receive application-specific recommendations—not one-size-fits-all solutions. Whether you’re evaluating internals for a sour water stripper or a high-purity benzene splitter, experienced engineers can tailor design upgrades, material selection, and installation practices to your exact process. Partnering early in the evaluation stage can prevent costly errors during turnaround or retrofitting projects.
With over 70 years of engineering excellence, AMACS provides high-performance internals for separation and mass transfer applications in refining, petrochemical, chemical, and gas processing industries. Our team delivers not only custom-designed trays and packing systems, but also application-specific diagnostics, retrofitting guidance, and 24/7 emergency support.
Ready to boost performance, reduce energy costs, and improve column reliability?
Contact AMACS today and let our technical experts help you engi